Medium and high temperature solder adhesive (epoxy solder paste) is a solder using SnAgCu alloy and SnSb alloy as metal filler particles. Compared with medium and high temperature solder paste, epoxy resin or silicone resin is used to replace rosin resin. The application of solder adhesive is the same as solder paste. After reflow, the alloy powder and soldering pad are metallurgically connected. Resin component cures and becomes thermoset adhesive around solder joints, which makes it unnecessary to clean. The thermoset adhesive reinforces and boosts the electrical performance of solder joints. Solder adhesive is a new type of electronic packaging material.
FSA-305P
FSA-901P/D
FSA-305D
FSA-305P series medium-temperature ultra-fine solder paste products (epoxy SAC solder paste) are composed of SAC305 solder powder and halogen-free flux. The amount of solvent evaporate can be reduced during soldering and solidifying. There is no solder ball formation after soldering. The solder joints are metallurgical connections, which are equivalent to the soldering effect of solder paste. Compared with rosin solder paste, the solder residue of FSA-305P becomes thermosetting adhesive to strengthen the solder joint and enhance the anti-corrosion and insulation performance. FSA-305P is a no-clean and superior solder for medium-temperature soldering.
1. Before Curing:
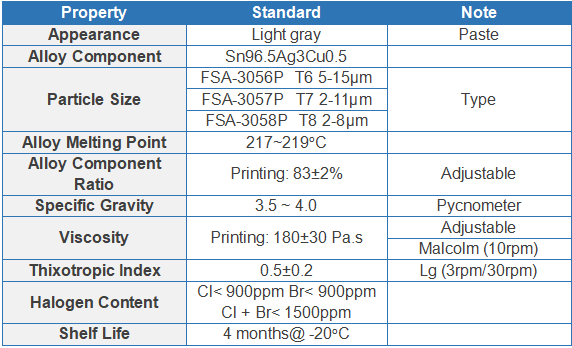
2. After Curing:
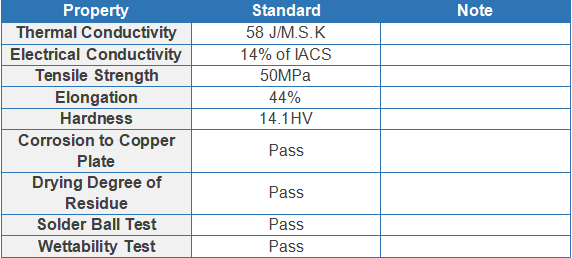
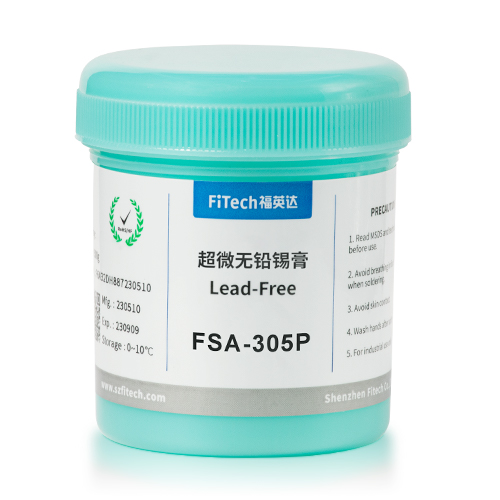
Warming Method: The sealed solder paste should rewarm to room temperature naturally; Rewarm no more than twice.
Warming Time: Rewarm 2 to 3 hours at room temperature. The actual time required to reach thermal equilibrium varies by vessel size.
Note: Do not open the bottle cap without sufficient rewarming or shorten the rewarming time by using heating equipment.
Operating Environment: The best operating temperature and humidity are 20-25°C and 40-50%RH, respectively. Reflow soldering in a nitrogen atmosphere is recommended.
Stencil Cleaning Solvent: Ether. Propylene glycol monomethyl ether (PM) is preferred.
FSA-901 series epoxy solder paste is composed of high-temperature Sn90Sb10 solder powder and halogen-free flux. Only a tiny amount of solvent evaporates during the soldering and solidification process. There is no solder ball formation after soldering. The solder powder melts and shrinks, and the solder joints are metallurgical connections, which are equivalent to the soldering effect of solder paste. FSA-901 epoxy solder paste is unnecessary to clean. The solder residue becomes thermosetting adhesive to reinforce the solder joints and enhance the anti-corrosion and insulation performance. The product is excellent for high-temperature soldering.
1. Before Curing:
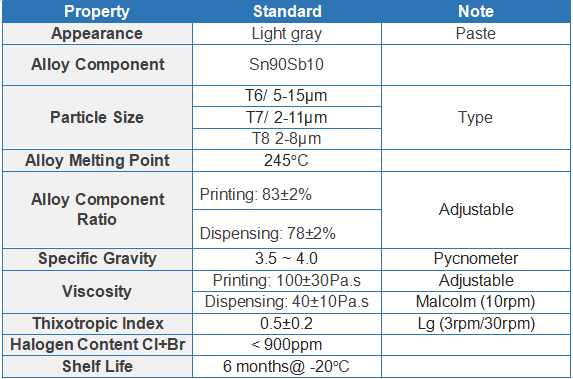
2. After Curing:
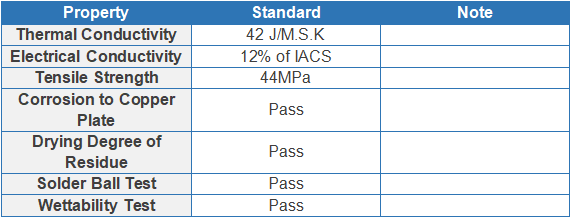
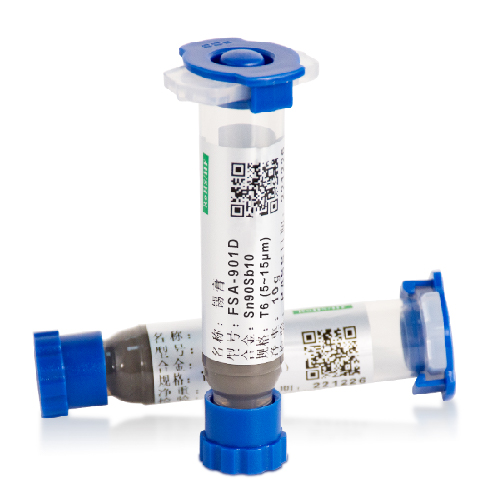
Warming Method: The sealed solder paste should rewarm to room temperature naturally; Rewarm no more than twice.
Warming Time: Rewarm 2 to 3 hours at room temperature. The actual time required to reach thermal equilibrium varies by vessel size.
Note: Do not open the bottle cap without sufficient rewarming or shorten the rewarming time by using heating equipment.
Operating Environment: The best operating temperature and humidity are 20-25°C and 40-50%RH, respectively. Reflow soldering in a nitrogen atmosphere is recommended.
Stencil Cleaning Solvent: Ether. Propylene glycol monomethyl ether (PM) is preferred.
FSA-305D series medium-temperature fine-pitch ultra-fine solder paste (SnAgCu epoxy solder paste) is composed of SAC305 solder powder and halogen-free flux. Only a tiny amount of solvent evaporates during the soldering and solidification process. There is no solder ball formation after soldering. The solder powder melts and shrinks, and the solder joints are metallurgical connections, which are equivalent to the soldering effect of solder paste. Compared with rosin solder paste, the solder residue becomes thermosetting adhesive to enhance the solder joint strength, corrosion resistance, and insulation. FSA-305 is a type of no-clean solder paste. It is a superior solder for medium temperature soldering.
1. Before Curing:
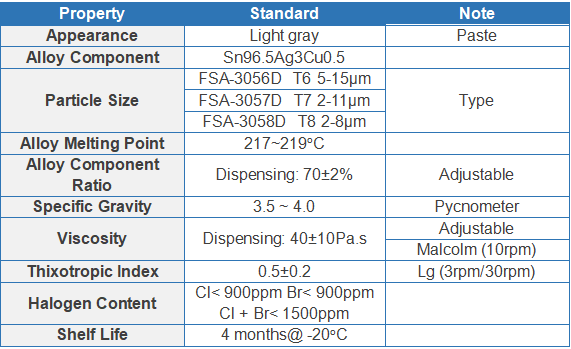
2. After Curing:
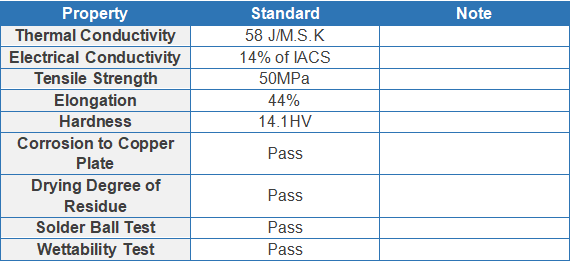
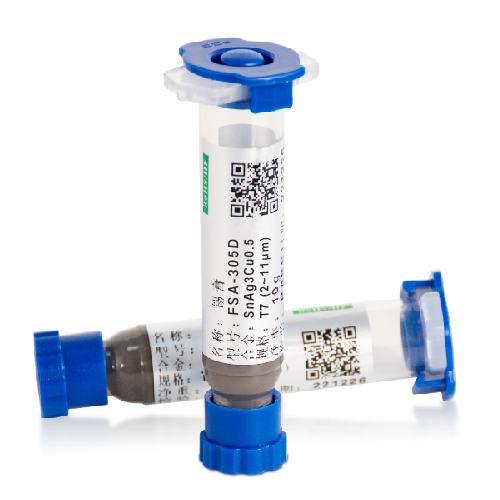
Warming Method: The sealed solder paste should rewarm to room temperature naturally; Rewarm no more than twice.
Warming Time: Rewarm 2 to 3 hours at room temperature. The actual time required to reach thermal equilibrium varies by vessel size.
Note: Do not open the bottle cap without sufficient rewarming or shorten the rewarming time by using heating equipment;
Operating Environment: The best operating temperature and humidity are 20-25°C and 40-50%RH, respectively. Reflow soldering in a nitrogen atmosphere is recommended.
Stencil Cleaning Solvent: Ether. Propylene glycol monomethyl ether (PM) is preferred.