No-clean solder paste is a kind of solder paste developed from solvent-soluble solder paste. The substrate packaged with no-clean solder paste does not undergo a cleaning process. Due to the use of the tiny amount of corrosive or non-corrosive active substances, the residue produced is no-corrosive. Hence, the solder paste can successfully pass the electrical performance test, achieving the purpose of no cleaning. Importantly. Solder paste after soldering is required to have superior performance, such as residue reduction, no corrosion, residue dryness, suitable surface insulation resistance, and anti-electromigration. Most solder pastes on the market are no-clean solder pastes, which have outstanding stability and are easy to use.
FTJ-901
FSA-170D
FTD/FTP-017
FTP-574
FTD/FTP-007
FSA-305D
FTD-170
FTD-901
FTJ-305
FTJ-574
FTD-574
FTD-305
FH-280
FH-260D
FSA-574D
FTP-305
FTP-170
FH-260P
FTP-901
The main alloy component of FSA-170D series epoxy solder paste is Fitech’s FL170 low-temperature alloy solder powder (SnBiAgX). Fitech classifies FL170 solder powders into T4 to T7 based on particle sizes. The solder powder and epoxy-based flux are formulated into superior low-temperature high-reliability solder paste.
1. Excellent sphericity, uniform particle size, low oxygen content, and high strength;
2. Reduce solvent volatilization during the solidification process;
3. Halogen-free formula;
4. Reduce solder ball formation after soldering;
5. The solder joints are metallurgically connected, which are equivalent to the soldering effects of solder paste;
6. The soldering residue becomes thermosetting adhesive, which is attached around the solder joint to improve its strength and enhance the anti-corrosion and insulation performance;
7. No cleaning necessary;
8. It is suitable for reliable packaging of thin substrates and non-heat-resistant components.
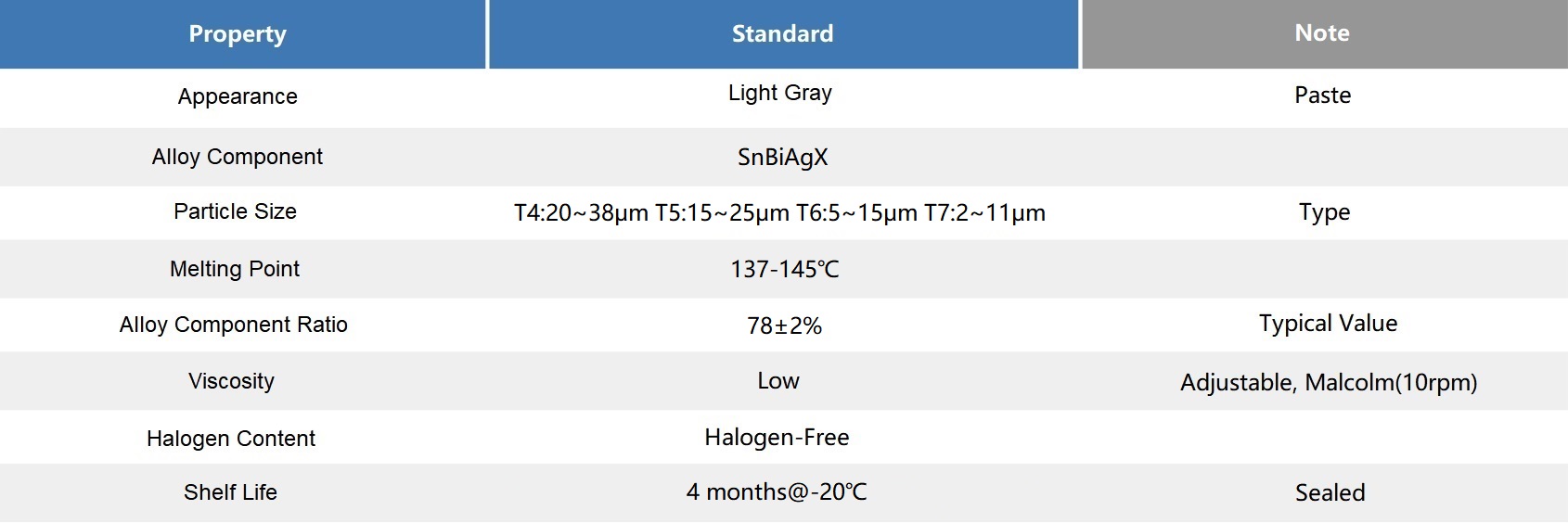

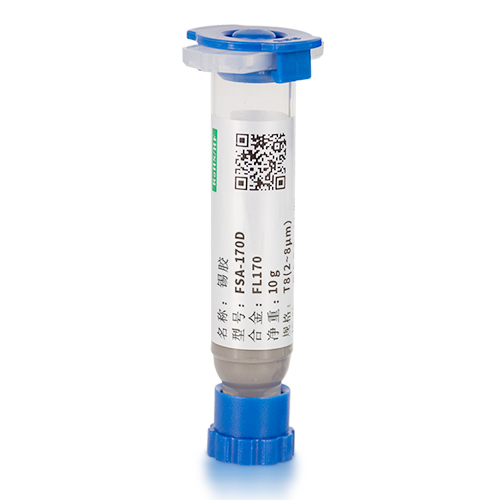
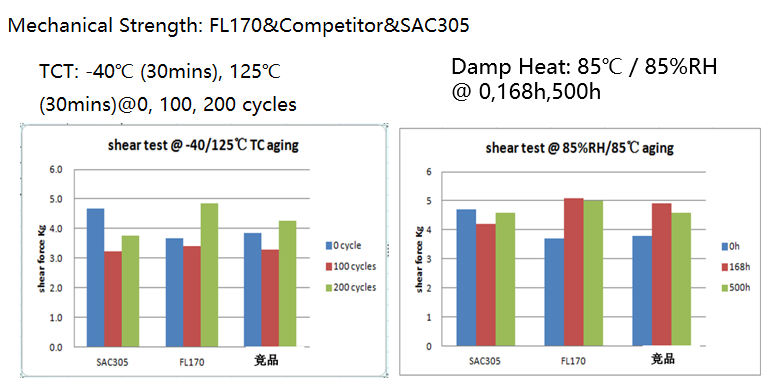
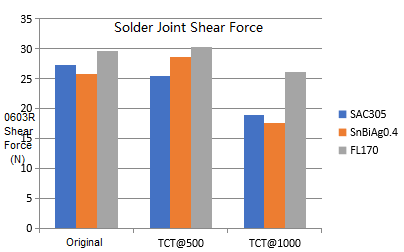
Warming Method: The sealed solder paste should rewarm to room temperature naturally; Rewarm no more than twice.
Warming Time: Rewarm 2 to 3 hours at room temperature. The actual time required to reach thermal equilibrium varies by vessel size.
Note: Do not open the bottle cap without sufficient rewarming or shorten the rewarming time by using heating equipment.
Operating Environment: The best operating temperature and humidity are 20-25°C and 40-60%RH, respectively. Reflow soldering in a nitrogen atmosphere is recommended.
Stencil Cleaning Solvent: Ether. Propylene glycol monomethyl ether (PM) is preferred.
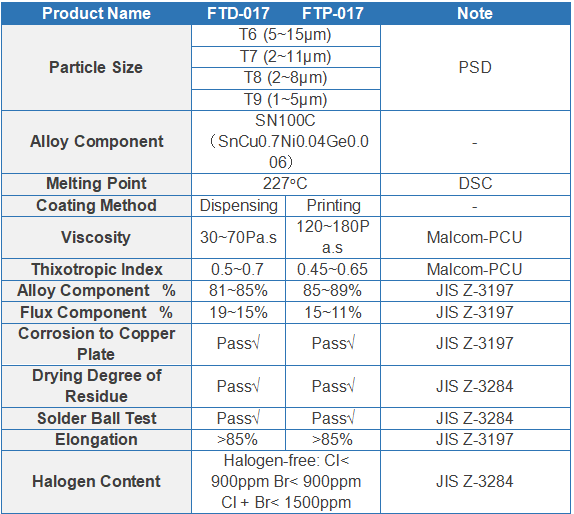
1. Peak reflow temperature: 25-45°C above melting temperature;
2. Type 5 solder reflows under nitrogen protection (oxygen content<200PPM);
3. Type 6 solder reflows under nitrogen protection (oxygen content<100PPM);
4. Store at 0-10°C.
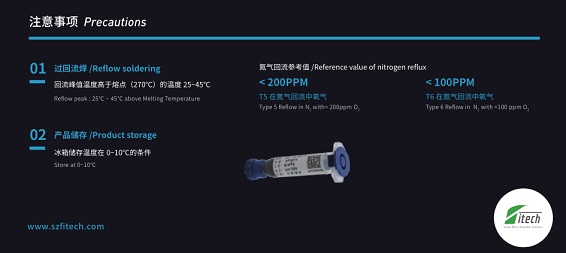
Fitech's tin-bismuth-silver alloy solder powder with excellent sphericity, uniform particle size, and low oxygen content is mixed with excellent zero-halogen flux to prepare FTP-574 series low-temperature solder paste. Solvent volatilizes very slightly during soldering. There is no solder ball formation and only a small amount of residue forms after soldering. Moreover, the product has outstanding wettability, and the solder joints generated are plump and bright. It is effective for low-temperature component mounting.
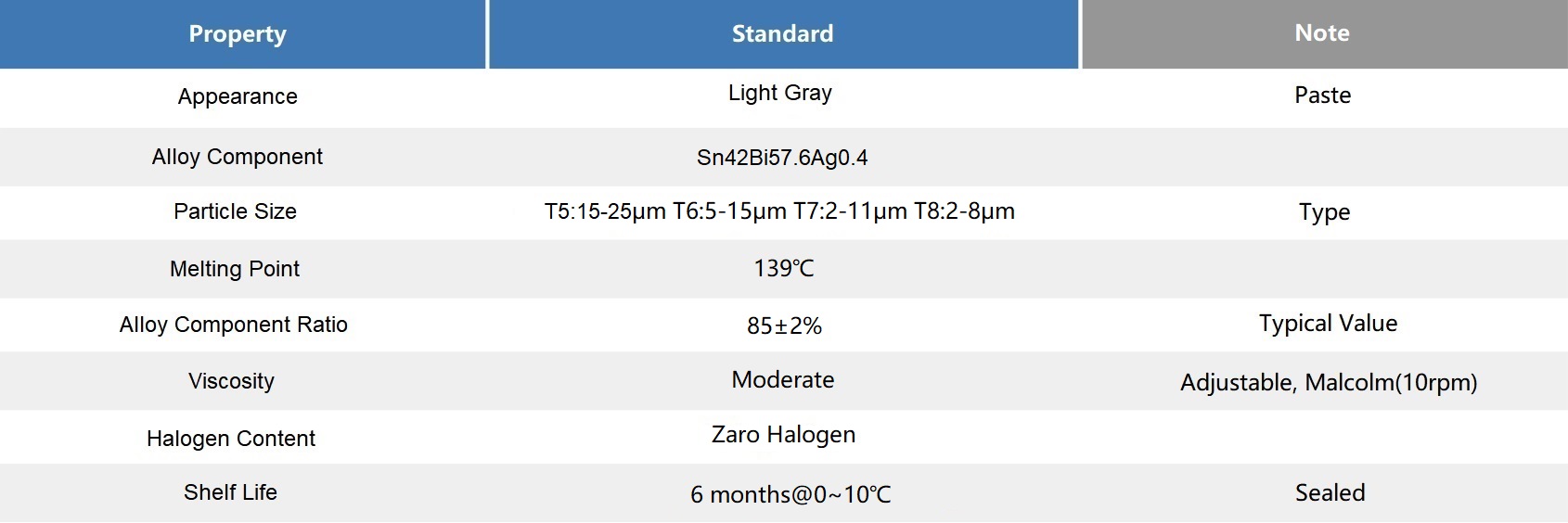
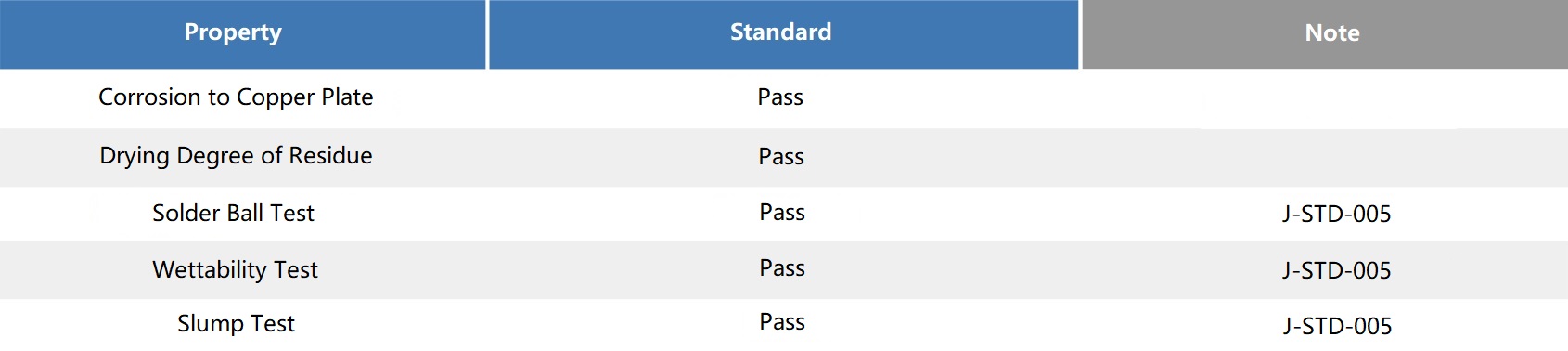
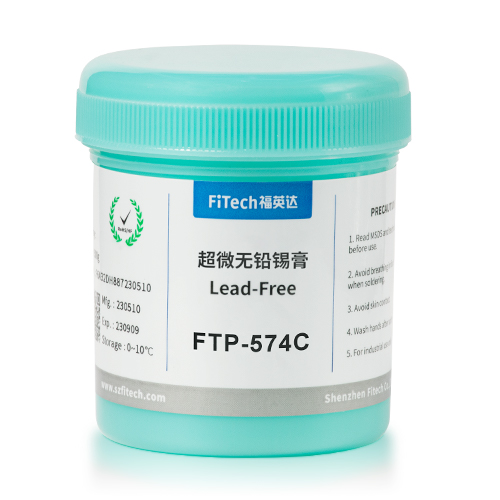
1. Warming Instruction: Solder paste needs to be refrigerated, and the preferred temperature is 0-10°C. When the solder paste is taken out from the cold box, its temperature is much lower than the room temperature. If the bottle cap is opened without rewarming, the water vapor in the air will easily condense and adhere to the solder paste. The high temperature exceeding 150°C during soldering increases vaporizatipn of water, which may cause the phenomenon of "exploding solder" to produce solder balls and even damage the components.
2. Warming Method: The sealed solder paste should rewarm to room temperature naturally; Rewarm no more than twice.
3. Warming Time: Return to warm for 2 to 3 hours at room temperature. The actual time required to reach thermal equilibrium varies by vessel size.
4. Note: Do not open the bottle cap without sufficient rewarming or shorten the rewarming by using heat equipment.
5. Operating Environment:The best operating temperature and humidity are 20-25°C and 40-50%RH, respectively. Reflow soldering in a nitrogen atmosphere is recommended.
6. Operating Time
① Continuous printing time: When adding solder paste continuously: 8 hours; In case of discontinuous addition of solder paste: 4 hours; ② Please add solder paste before the solder paste on the board is almost one third (rolling diameter: 10mm or less); ③ Please keep the solder paste on the plate within 3 hours; ④ If printing is interrupted for more than 30 minutes, please clean the stencil. ⑤ Dwell time after printing: After the solder paste is printed, the components should be mounted as soon as possible and the soldering should be completed when passing the oven to avoid drying out the surface of the solder paste due to long storage, which will affect the component mounting and soldering effects. Generally, the recommended dwell time of solder paste is no more than 4 hours, while the low temperature bismuth-containing solder paste does not exceed 2 hours. If the printing is interrupted for more than 30 minutes or is temporarily interrupted, the printing template needs to be cleaned. It can continue to work after 1-2 trial printing. The solder paste attached to narrow space of the opening (≤0.4mm) and the opening of the stencil will gradually dry, which will degenerate the adhesive ability.
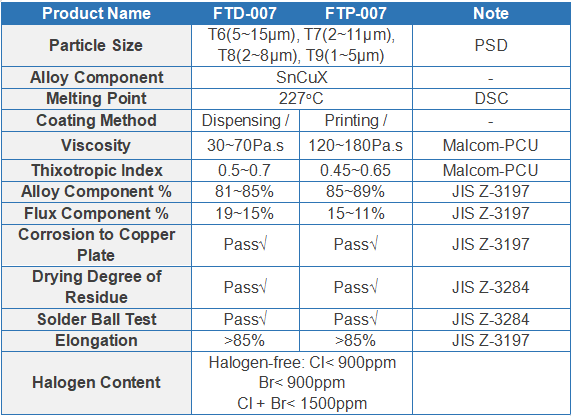
1. Peak reflow temperature: 25-45°C above the melting temperature;
2. Type 5 solder reflows under nitrogen protection (oxygen content<200PPM);
3. Type 6 solder reflows under nitrogen protection (oxygen content<100PPM);
4. Store at 0-10°C.
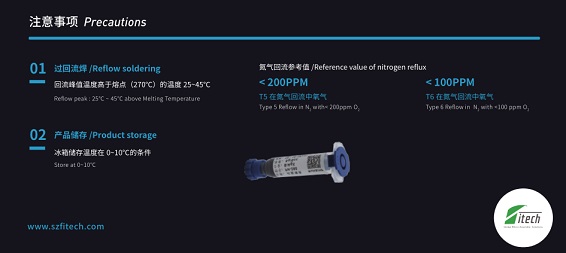
FSA-305D series medium-temperature fine-pitch ultra-fine solder paste (SnAgCu epoxy solder paste) is composed of SAC305 solder powder and halogen-free flux. Only a tiny amount of solvent evaporates during the soldering and solidification process. There is no solder ball formation after soldering. The solder powder melts and shrinks, and the solder joints are metallurgical connections, which are equivalent to the soldering effect of solder paste. Compared with rosin solder paste, the solder residue becomes thermosetting adhesive to enhance the solder joint strength, corrosion resistance, and insulation. FSA-305 is a type of no-clean solder paste. It is a superior solder for medium temperature soldering.
1. Before Curing:
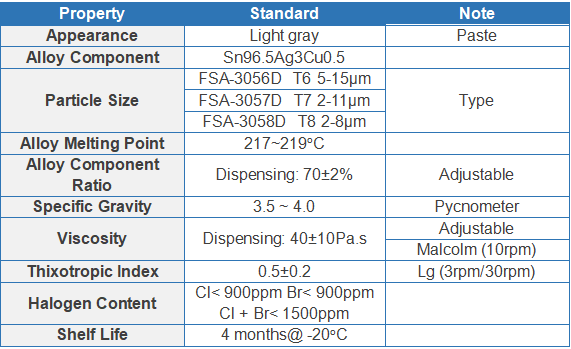
2. After Curing:
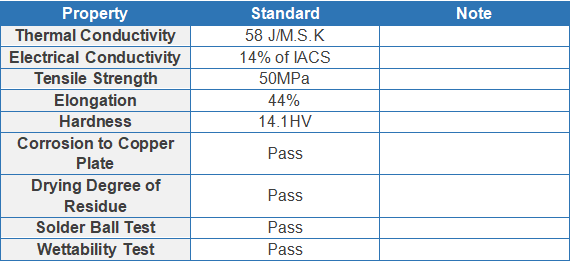
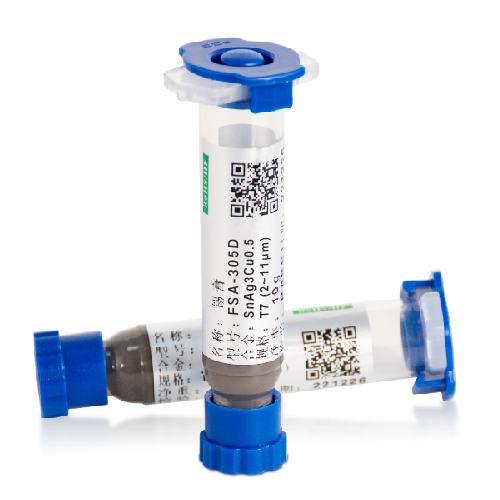
Warming Method: The sealed solder paste should rewarm to room temperature naturally; Rewarm no more than twice.
Warming Time: Rewarm 2 to 3 hours at room temperature. The actual time required to reach thermal equilibrium varies by vessel size.
Note: Do not open the bottle cap without sufficient rewarming or shorten the rewarming time by using heating equipment;
Operating Environment: The best operating temperature and humidity are 20-25°C and 40-50%RH, respectively. Reflow soldering in a nitrogen atmosphere is recommended.
Stencil Cleaning Solvent: Ether. Propylene glycol monomethyl ether (PM) is preferred.
Low-temperature FL170 alloy solder powder with good sphericity, uniform particle size, low oxygen content, and high strength are combined with zero-halogen flux to produce FTD-170 series low-temperature solder paste. Only a small amount of solvent volatilizes during the soldering process. There is no solder ball formation after soldering. The solder paste has excellent performance of residue minimization and wettability. The solder joints generated are strong, plump, and bright. FTD-170 is ideal for low-temperature soldering, especially for low-temperature component mounting.
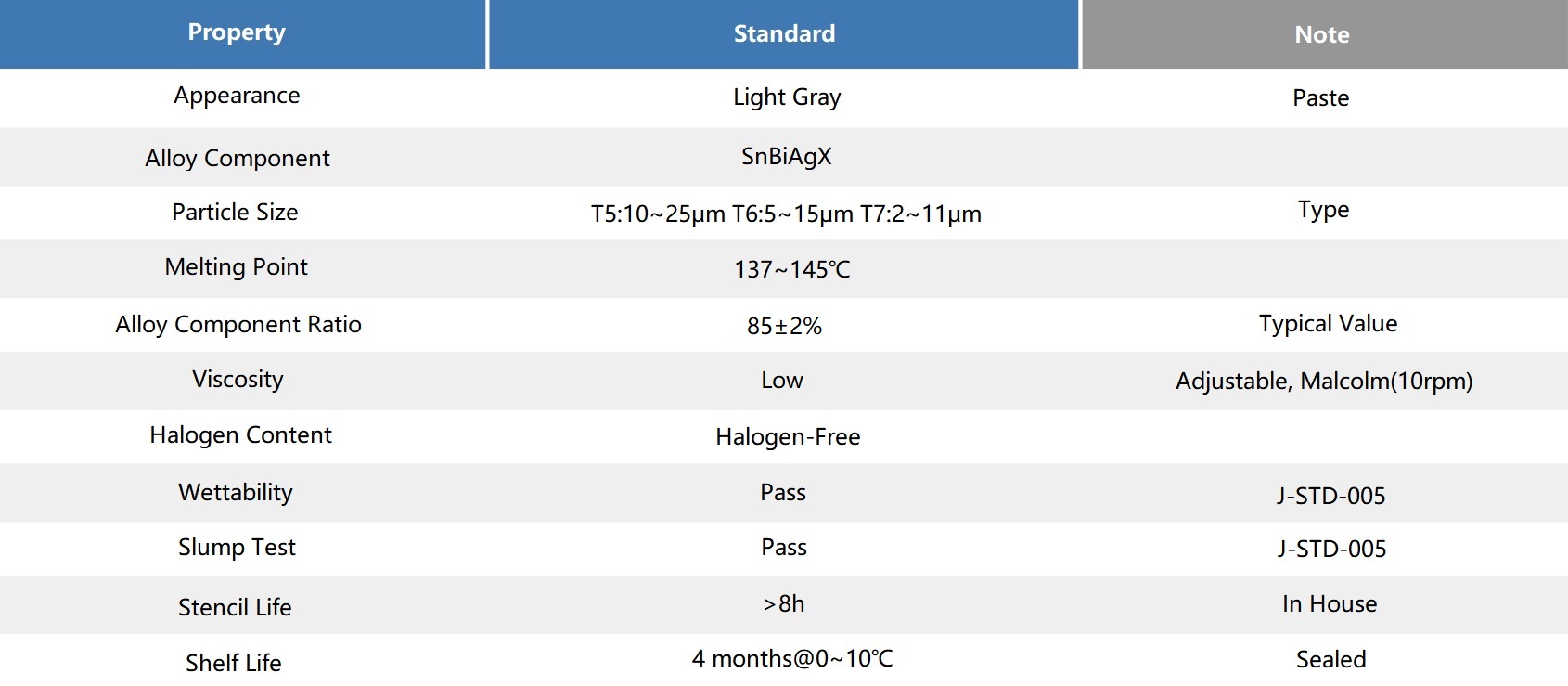

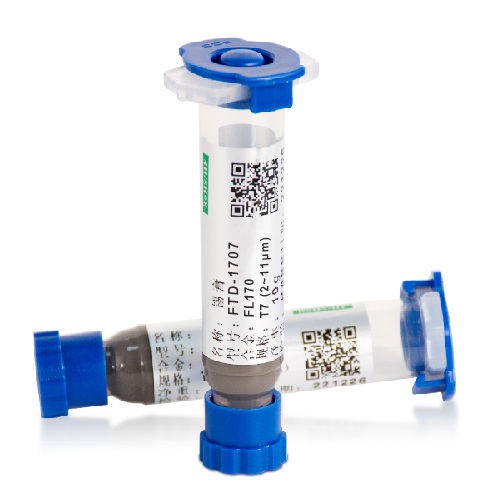
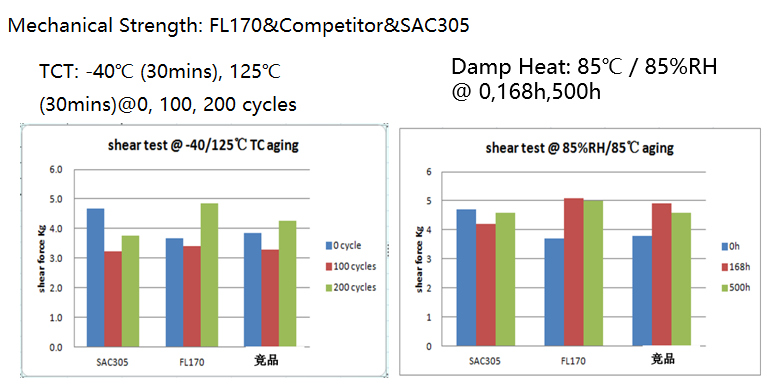
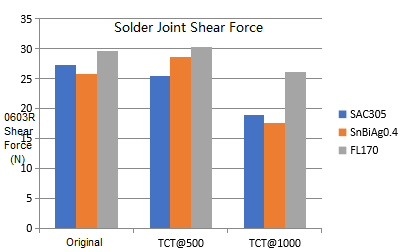
1. Warming Instruction: Solder paste needs to be refrigerated, and the preferred temperature is 0-10°C. When taking out the solder paste from the cold box, its temperature is much lower than the room temperature. If the bottle cap is opened without rewarming, the water vapor in the air will easily condense and adhere to the solder paste.The high temperature exceeding 150°C during soldering increases the vaporization of water, which may cause the phenomenon of "exploding solder" to produce solder balls and even damage the components.
2. Warming Method: The sealed solder paste should rewarm to room temperature naturally; Rewarm no more than twice.
3. Warming Time: Return to warm for 2 to 3 hours at room temperature. The actual time required to reach thermal equilibrium varies by vessel size.
4. Note: Do not open the bottle cap without sufficient rewarming or shorten the rewarming time by using heat sources.
5. Operating Environment: The best operating temperature and humidity are 20-25°C and 40-60%RH, respectively. Reflow soldering in a nitrogen atmosphere is recommended.
6. Operating Time
① Continuous printing time: When adding solder paste continuously: 8 hours; In case of discontinuous addition of solder paste: 4 hours; ② Please add solder paste before the solder paste on the board is almost one third (rolling diameter: 10mm or less); ③ Please keep the solder paste on the plate within 3 hours; ④ If printing is interrupted for more than 30 minutes, please clean the stencil. ⑤ Dwell time after printing: After the solder paste is printed, the components should be mounted as soon as possible and the soldering should be completed when passing the oven to avoid drying out the surface of the solder paste due to long storage, which will affect the component mounting and soldering effects. Generally, the recommended dwell time of solder paste is no more than 4 hours, while the low-temperature bismuth-containing solder paste does not exceed 2 hours. If the printing is interrupted for more than 30 minutes or is temporarily interrupted, the printing template needs to be cleaned. It can continue to work after 1-2 trial printing. The solder paste attached to the narrow space of the opening (≤0.4mm) and the opening of the stencil will gradually dry, which will degenerate the adhesive ability.
SnSb10 alloy solder powder with excellent sphericity, uniform particle size, and low oxygen content is mixed with no-clean flux to produce FTD-901 series solder paste based on metallurgical method and chemical structure. The solder paste has a superior adhesion effect before soldering. Solvent volatilizes very slightly during soldering. Moreover, FTD-901 has outstanding wettability, anti-slump, and residue reduction properties. It is developed to meet the market demand for heat-resistant microelectronic assembly and precision soldering. The product has extraordinary heat resistance and heat dissipation abilities. It also improves the voiding of solder joints and the strength and conductivity of intermetallic compounds.
1. Before Curing:
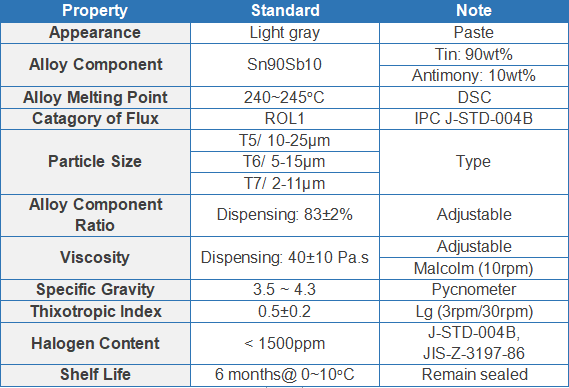
2. After Curing:
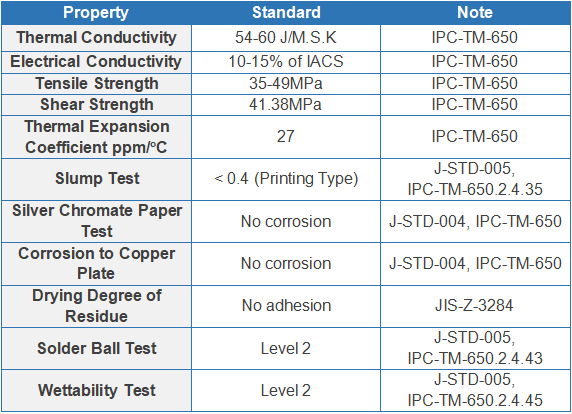
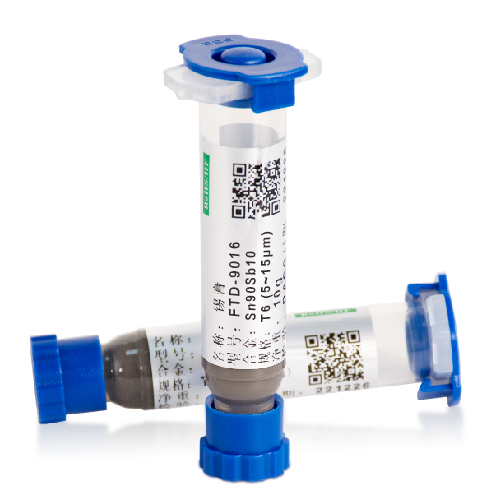
Warming Method: The sealed solder paste should rewarm to room temperature naturally; Rewarm no more than twice.
Warming Time: Return to warm for 2 to 3 hours at room temperature. The actual time required to reach thermal equilibrium varies by vessel size.
Note: Do not open the bottle cap without sufficient rewarming or shorten the rewarming time by using heating equipment.
Operating Environment: The best operating temperature and humidity are 20-25°C and 40-50%RH, respectively. Reflow soldering in a nitrogen atmosphere is recommended.
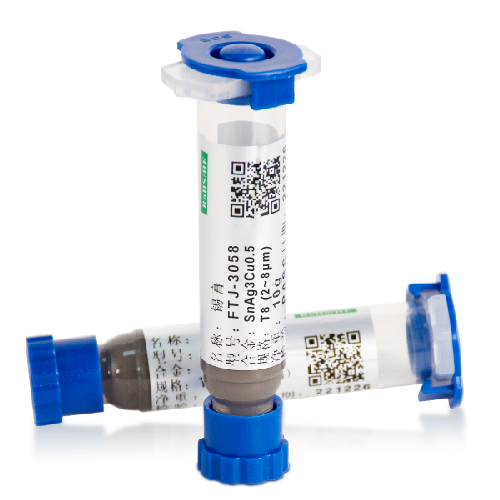
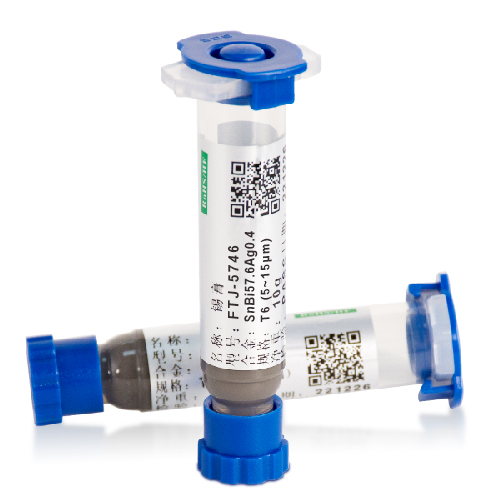
Fitech’s tin-bismuth-silver solder powder with excellent sphericity, uniform particle size, and low oxygen content is mixed with excellent zero-halogen flux to prepare FTD-574 series low-temperature solder paste. Solvent volatilizes very slightly during soldering. There is no solder ball formation during soldering, and only a small amount of residue is produced after soldering. Moreover, FTD-574 has outstanding wettability. The solder joints generated are plump and bright. The product is effective for low-temperature component mounting.
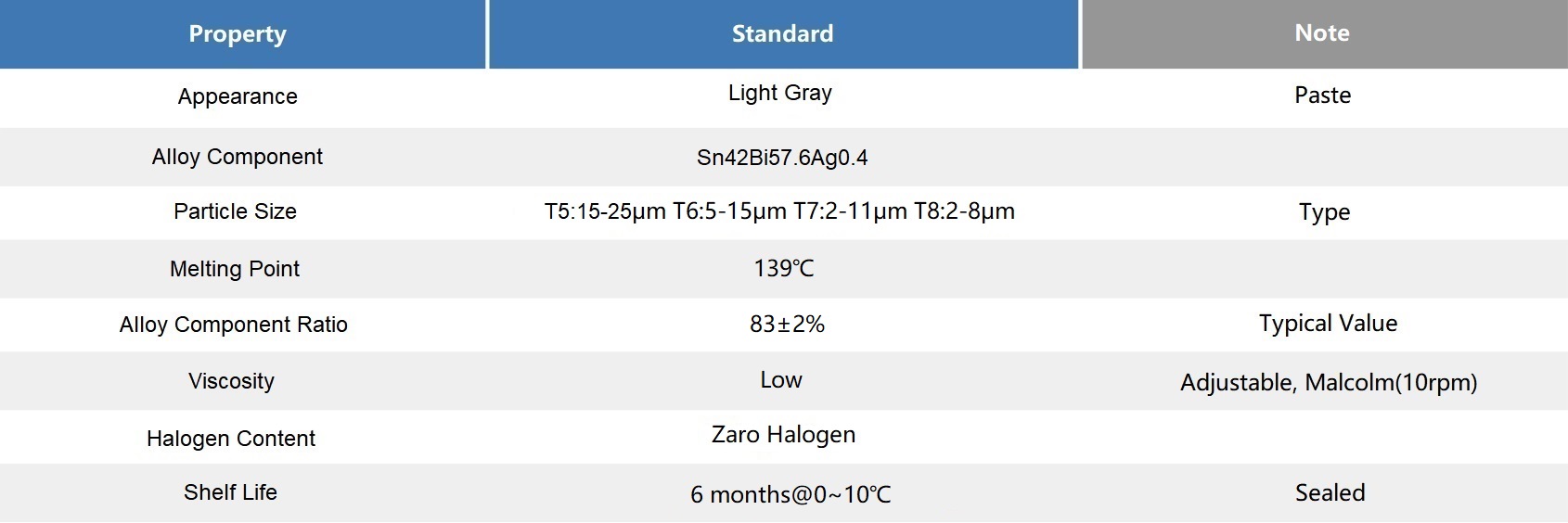
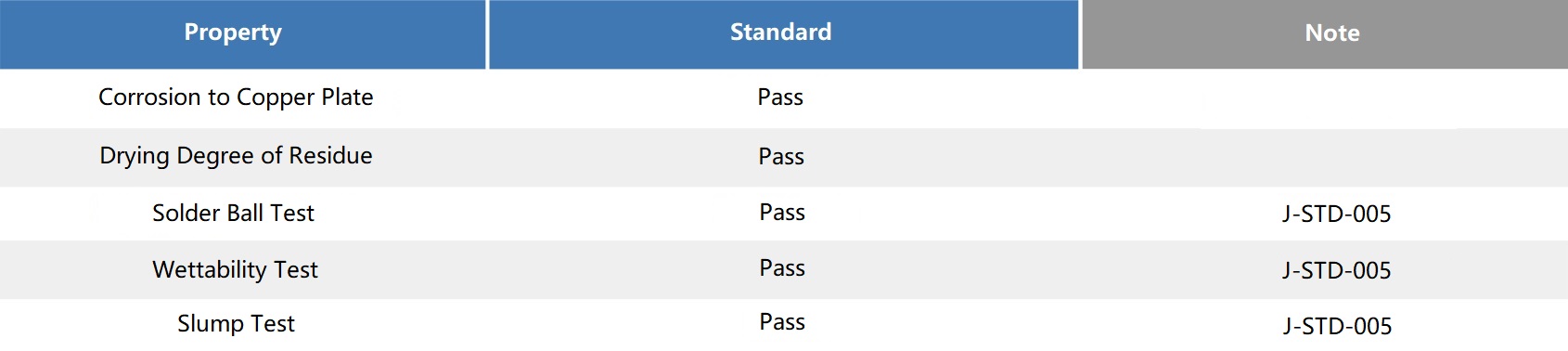
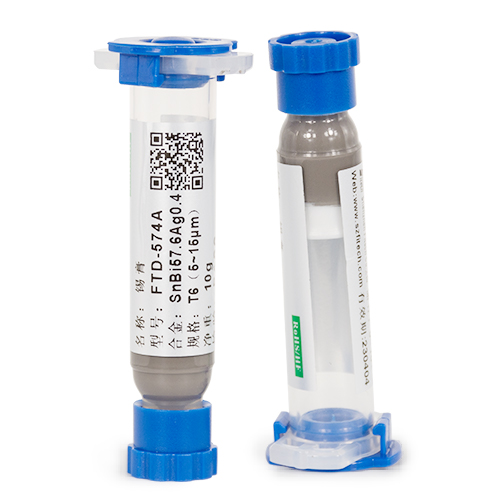
1. Warming Instruction: Solder paste usually needs to be refrigerated, and the preferred temperature is 0-10°C. When taking out the solder paste from the cold box, its temperature is much lower than the room temperature. If the bottle cap is opened without rewarming, the water vapor in the air will easily condense and adhere to the solder paste. The high temperature exceeding 150°C during soldering increases the vaporization of water, which may cause the phenomenon of "exploding solder" to produce solder balls and even damage the components.
The temperature exceeds 150℃), the water vaporizes rapidly due to the strong heat, which is easy to cause the phenomenon of "exploding tin" to produce tin beads and even damage the components.
温度超过150℃),水受强热迅速汽化,易造成“爆锡”现象产生锡珠,甚至损坏元器件。
The temperature exceeds 150℃), the water vaporizes rapidly due to the strong heat, which is easy to cause the phenomenon of "exploding tin", resulting in tin beads and even damage to the components.
温度超过150℃),水受强热迅速汽化,易造成“爆锡”现象,产生锡珠,甚至损坏元器件。
无法加载全部结果
重试
正在重试…
正在重试…
无法加载全部结果
重试
正在重试…
正在重试…
2. Warming Method: The sealed solder paste should rewarm to room temperature naturally; Rewarm no more than twice.
2. Warming method: Under the premise of not opening the lid, return to temperature naturally at room temperature; the number of times of returning to temperature is no more than twice;
2、升温方法:在不开盖的前提下,在室温下自然回温;回温次数不超过两次;
2. Warming method: Under the premise of not opening the lid, return to temperature naturally at room temperature; the number of times of returning to temperature is no more than two times;
2、升温方法:在不开盖的前提下,在室温下自然回温;回温次数不超过2次;
无法加载全部结果
重试
正在重试…
正在重试…
无法加载全部结果
重试
正在重试…
正在重试…
3. Warming Time: Return to warm for 2 to 3 hours at room temperature. The actual time required to reach thermal equilibrium varies by vessel size.
The actual time required to reach thermal equilibrium varies by vessel size.
达到热平衡所需的实际时间因容器尺寸而异。
The actual time required to reach thermal equilibrium will vary depending on the size of the vessel.
达到热平衡所需的实际时间将根据容器的大小而有所不同。
无法加载全部结果
重试
正在重试…
正在重试…
无法加载全部结果
重试
正在重试…
正在重试…
4. Note: Do not open the bottle cap without sufficient rewarming or shorten the rewarming time by using heating equipment.
Note: Do not open the bottle cap without sufficient "rewarming", and do not shorten the "rewarming" time by heating;
注意:没有充分“复温”就不要打开瓶盖,也不要通过加热来缩短“复温”时间;
Note: Do not open the bottle cap without sufficient "rewarming", and the "rewarming" time cannot be shortened by heating;
注意:没有充分“复温”就不要打开瓶盖,加热不能缩短“复温”时间;
无法加载全部结果
重试
正在重试…
正在重试…
无法加载全部结果
重试
正在重试…
正在重试…
The actual time required to reach thermal equilibrium varies by vessel size.
达到热平衡所需的实际时间因容器尺寸而异。
The actual time required to reach thermal equilibrium will vary depending on the size of the vessel.
达到热平衡所需的实际时间将根据容器的大小而有所不同。
无法加载全部结果
重试
正在重试…
正在重试…
无法加载全部结果
重试
正在重试…
正在重试…
4. Note: Do not open the bottle cap without sufficient "rewarming", and do not shorten the "rewarming" time by heating;
...
4. Note: Do not open the bottle cap without sufficient "rewarming", and the "rewarming" time cannot be shortened by heating;
...
无法加载全部结果
重试
正在重试…
正在重试…
无法加载全部结果
重试
正在重试…
正在重试…
5. Operating Environment:The best operating temperature and humidity are 20-25°C and 40-50%RH, respectively. Reflow soldering in a nitrogen atmosphere is recommended.
6. Operation Time
① Continuous printing time: When adding solder paste continuously: 8 hours. In case of discontinuous addition of solder paste: 4 hours; ② Please add solder paste before the solder paste on the board is almost one third (rolling diameter: 10mm or less); ③ Please keep the solder paste on the plate within 3 hours; ④ If printing is interrupted for more than 30 minutes, please clean the stencil; ⑤ Dwell time after printing: After the solder paste is printed, the components should be mounted as soon as possible and the soldering should be completed when passing the oven to avoid drying out the surface of the solder paste due to long storage, which will affect the component mounting and soldering effects. Generally, the recommended dwell time of solder paste is no more than 4 hours, while the low temperature bismuth-containing solder paste does not exceed 2 hours. If the printing is interrupted for more than 30 minutes or is temporarily interrupted, the printing template needs to be cleaned. It can continue to work after 1-2 trial printing. The solder paste attached to narrow space of the opening (≤0.4mm) and the opening of the stencil will gradually dry, which will degenerate the adhesive ability.
Fitech produces SAC305 solder powder with excellent sphericity, uniform particle size, and low oxygen content, and it is mixed with halogen-free flux to prepare FTD-305 series solder paste. The solder paste has superior adhesion before soldering. Solvent volatilizes very slightly during soldering. Moreover, FTD-305 has outstanding wettability, anti-slump, and residue reduction properties. There is no solder ball formation during soldering. The product is an ideal solder for micro-bump ultra-fine-pitch packaging.
1. Before Curing:
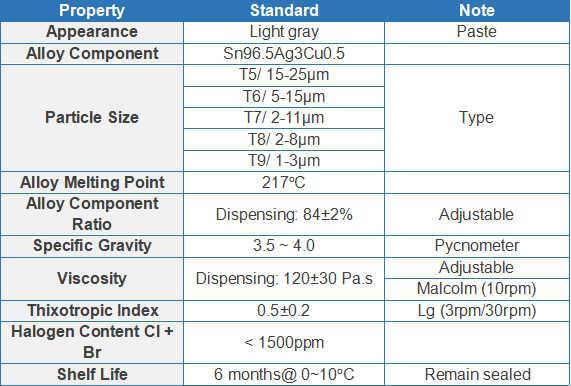
2. After Curing:
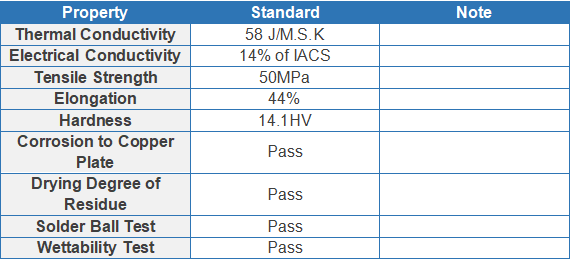
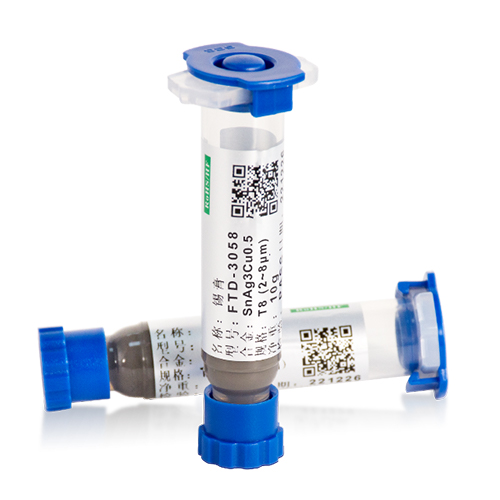
Product DIsplay of FTD-305 (Lead-Free Solder Paste for Dispensing)
Warming Method: The sealed solder paste should rewarm to room temperature naturally; Rewarm no more than twice.
Warming Time: Rewarm 2 to 3 hours at room temperature. The actual time required to reach thermal equilibrium varies by vessel size.
Note: Do not open the bottle cap without sufficient rewarming or shorten the rewarming time by using heating equipment.
Operating Environment: The best operating temperature and humidity are 20-25°C and 40-50%RH, respectively. Reflow soldering in a nitrogen atmosphere is recommended.
An80Sn20 solder powder with excellent sphericity, uniform particle size, and low oxygen content is combined with halogen-free flux to produce FH-280 series solder paste. FH-280 has a superior adhesion effect before soldering. Solvent volatilizes very slightly during soldering. In addition, the solder paste has outstanding wettability, anti-slump, and residue reduction properties. There is no solder ball formation during soldering. Moreover, FH-280 has high tensile strength, excellent corrosion resistance, high melting point, and extraordinary thermal creep performance. FH-280 is compatible with other precious metals and has excellent electrical and thermal conductivity. The product is suitable for the high-reliability packaging of semiconductors and microelectronic devices. It is applied to the high thermal conductivity packaging of high-power devices.
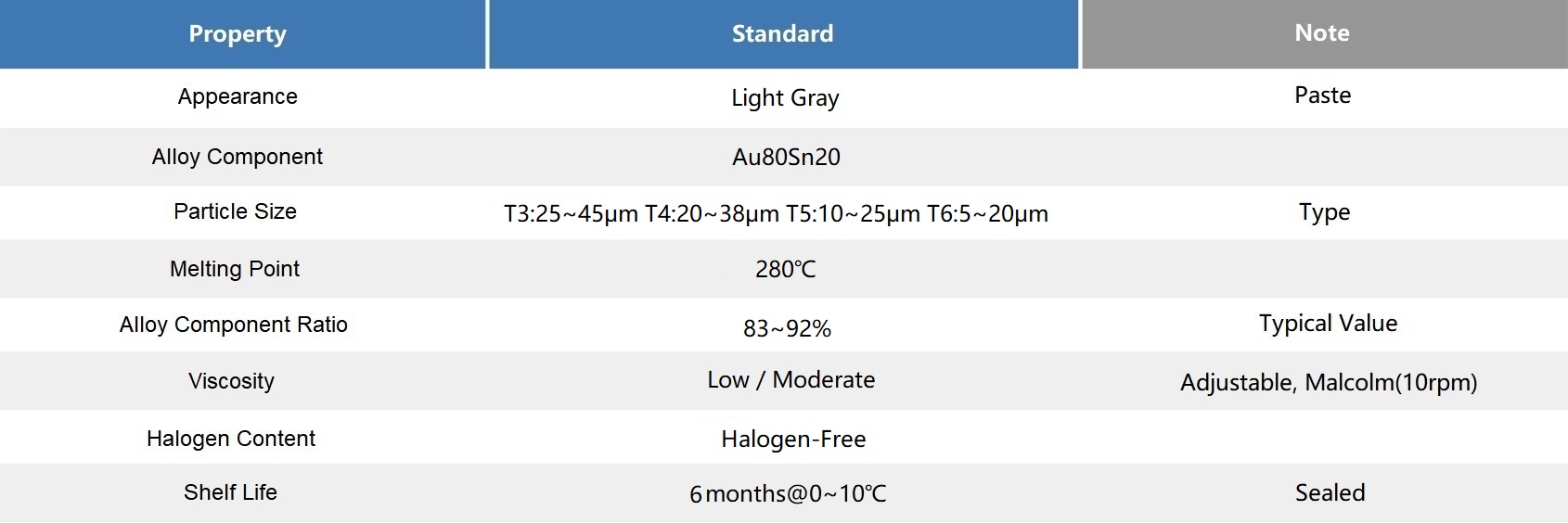

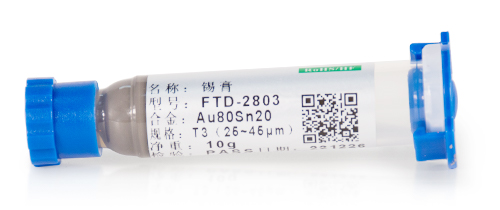
Warming Method: The sealed solder paste should rewarm to room temperature naturally; Rewarm no more than twice.
Warming Time: Rewarm 2 to 3 hours at room temperature. The actual time required to reach thermal equilibrium varies by vessel size.
Note: Do not open the bottle cap without sufficient rewarming or shorten the rewarming time by using heating equipment.
Operating Environment: The best operating temperature and humidity are 20-25°C and 40-60%RH, respectively. Reflow soldering in a nitrogen atmosphere is recommended.
FH-260 solder powder with excellent sphericity, uniform particle size, and low oxygen content is combined with halogen-free flux to produce FH-260D series solder paste. It is a high-temperature lead-free product developed for secondary reflow soldering of power semiconductor and microelectronic packaging. The alloy is synthesized based on bismuth elements by adding reinforced micro/nanoparticles, successfully replacing high-lead solder paste, and meeting RoHS environmental protection standards.
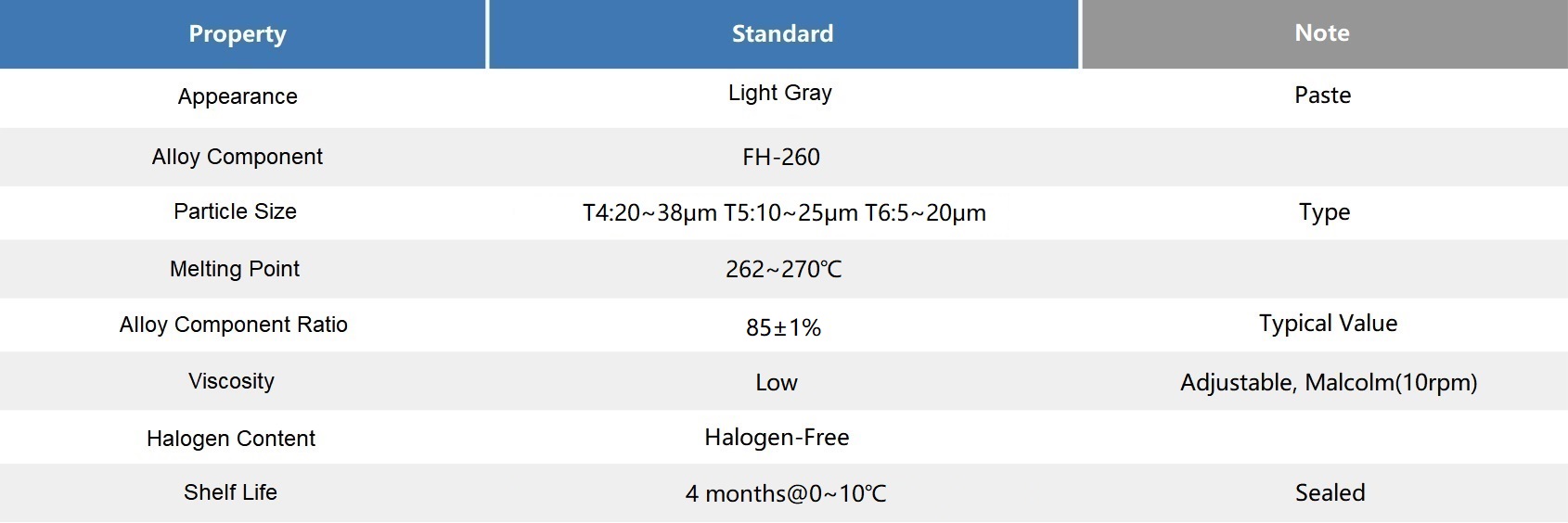

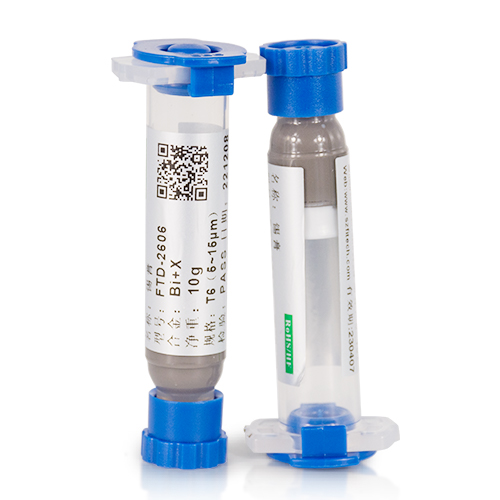
Warming Method: The sealed solder paste should rewarm to room temperature naturally; Rewarm no more than twice.
Warming Time: Rewarm 2 to 3 hours at room temperature. The actual time required to reach thermal equilibrium varies by vessel size.
Note: Do not open the bottle cap without sufficient rewarming or shorten the rewarming time by using heating equipment.
Operating Environment: The best operating temperature and humidity are 20-25°C and 40-60%RH, respectively. Reflow soldering in a nitrogen atmosphere is recommended.
FSA-574D series low-temperature lead-free epoxy solder paste is composed of low-temperature ultra-fine SnBi solder powder and halogen-free flux. Only a tiny amount of solvent evaporates during the soldering and solidification process. There is no solder ball formation after soldering. The solder powder melts and shrinks, and the solder joints are metallurgical connections, which are equivalent to the soldering effects of solder paste. FSA-574D epoxy solder paste is unnecessary to clean. Solder residue becomes thermosetting adhesive to reinforce the solder joints and enhance the anti-corrosion and insulation performance. FSA-574D is suitable for the reliable packaging of thin substrates and non-heat-resistant components.
1. Before Curing:
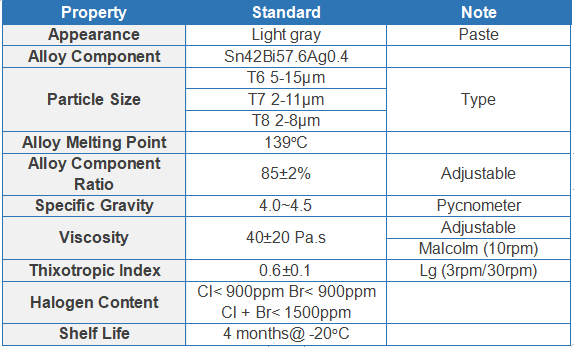
2. After Curing:
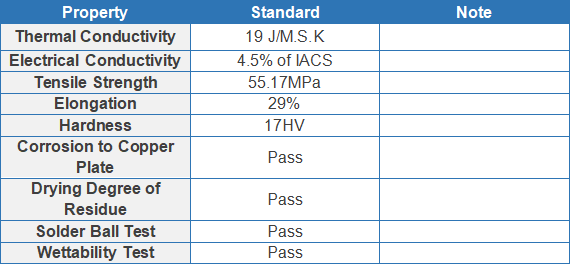
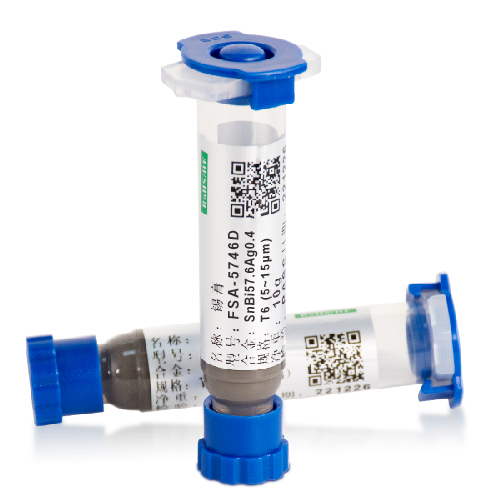
Warming Method: The sealed solder paste should rewarm to room temperature naturally; Rewarm no more than twice.
Warming Time: Rewarm 2 to 3 hours at room temperature. The actual time required to reach thermal equilibrium varies by vessel size.
Note: Do not open the bottle cap without sufficient rewarming or shorten the rewarming time by using heating equipment.
Operating Environment: The best operating temperature and humidity are 20-25°C and 40-50%RH, respectively. Reflow soldering in a nitrogen atmosphere is recommended.
Stencil Cleaning Solvent: Ether. Propylene glycol monomethyl ether (PM) is preferred.
Fitech produces SAC305 solder powder with excellent sphericity, uniform particle size, and low oxygen content, and it is mixed with halogen-free flux to prepare FTP-305 series solder paste. The solder paste has a superior adhesion effect before soldering. Solvent volatilizes very slightly during soldering. Moreover, FTP-305 has outstanding wettability, anti-slump, and residue reduction properties. There is no solder ball formation during soldering. The product is ideal for micro-bump ultra-fine-pitch packaging.
1. Before Curing:
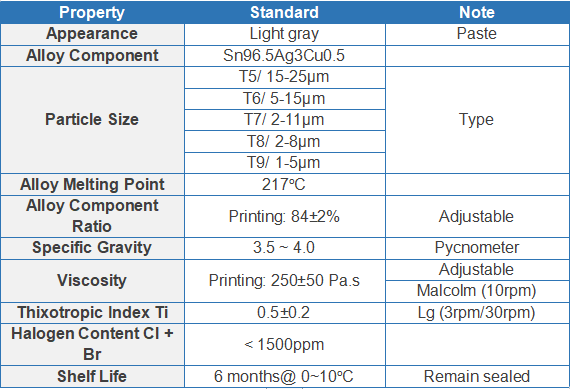
2. After Curing:
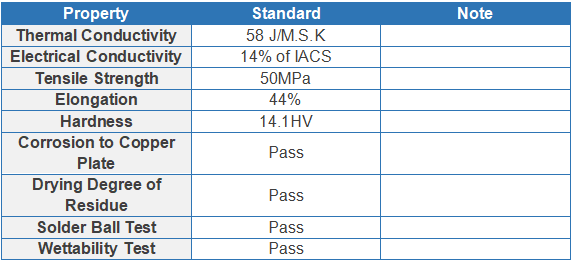
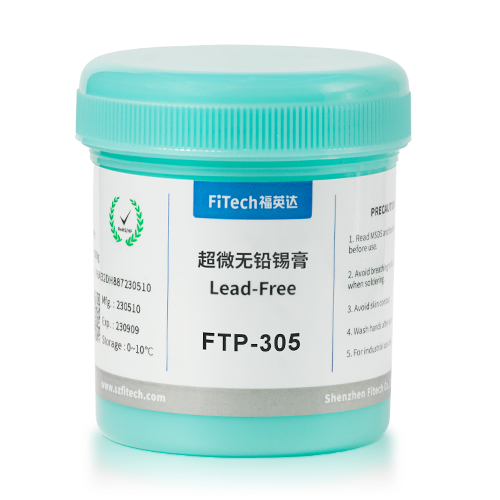
Warming Method: The sealed solder paste should rewarm to room temperature naturally; Rewarm no more than twice.
Warming Time: Rewarm 2 to 3 hours at room temperature. The actual time required to reach thermal equilibrium varies by vessel size.
Note: Do not open the bottle cap without sufficient rewarming or shorten the rewarming time by using heating equipment.
Operating Environment: The best operating temperature and humidity are 20-25°C and 40-50%RH, respectively. Reflow soldering in a nitrogen atmosphere is recommended.
Low-temperature FL170 alloy solder powder with excellent sphericity, uniform particle size, low oxygen content, and high strength are combined with zero-halogen flux to produce FTP-170 series low-temperature solder paste. Only a small amount of solvent volatilizes during the soldering process. There is no solder ball formation after soldering. In addition, FTP-170 has an excellent performance in residue minimization and wettability. The solder joints generated are strong, plump, and bright. The product is ideal for low-temperature soldering, especially for low-temperature component mounting.
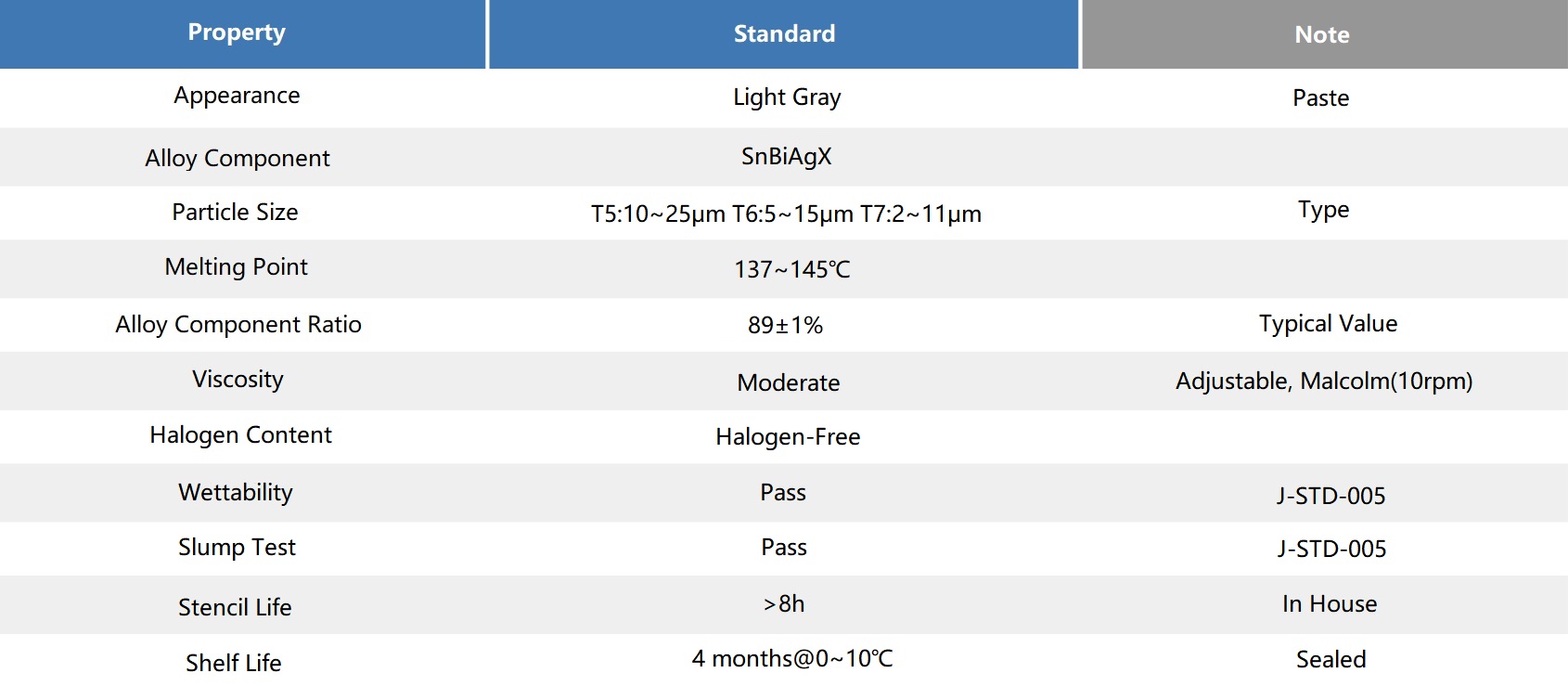

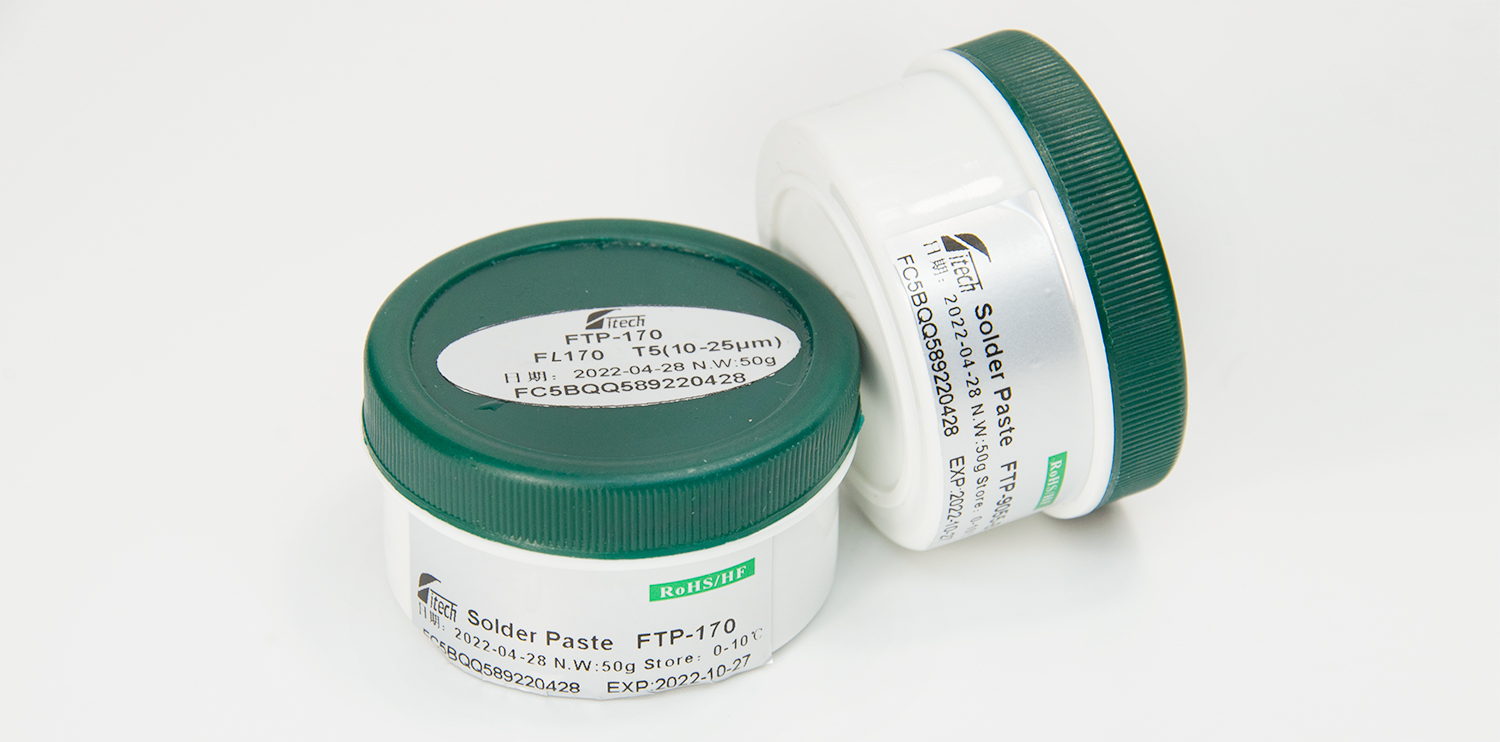
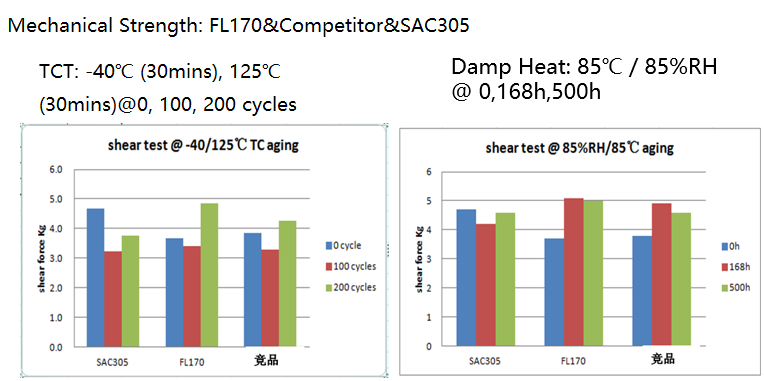
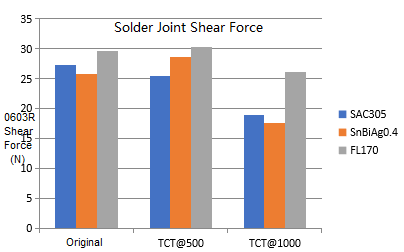
1. Warming Instruction: Solder paste needs to be refrigerated, and the preferred temperature is 0-10°C. When taking out the solder paste from the cold box, its temperature is much lower than the room temperature. If the bottle cap is opened without rewarming, the water vapor in the air will easily condense and adhere to the solder paste.The high temperature exceeding 150°C during soldering increases the vaporization of water, which may cause the phenomenon of "exploding solder" to produce solder balls and even damage the components.
2. Warming Method: The sealed solder paste should rewarm to room temperature naturally; Rewarm no more than twice.
3. Warming Time: Return to warm for 2 to 3 hours at room temperature. The actual time required to reach thermal equilibrium varies by vessel size.
4. Note: Do not open the bottle cap without sufficient rewarming or shorten the rewarming time by using heating equipment.
5. Operating Environment:The best operating temperature and humidity are 20-25°C and 40-60%RH, respectively. Reflow soldering in a nitrogen atmosphere is recommended.
6. Operating Time
① Continuous printing time: When adding solder paste continuously: 8 hours; In case of discontinuous addition of solder paste: 4 hours; ② Please add solder paste before the solder paste on the board is almost one third (rolling diameter: 10mm or less); ③ Please keep the solder paste on the plate within 3 hours; ④ If printing is interrupted for more than 30 minutes, please clean the stencil. ⑤ Dwell time after printing: After the solder paste is printed, the components should be mounted as soon as possible and the soldering should be completed when passing the oven to avoid drying out the surface of the solder paste due to long storage, which will affect the component mounting and soldering effects. Generally, the recommended dwell time of solder paste is no more than 4 hours, while the low temperature bismuth-containing solder paste does not exceed 2 hours. If the printing is interrupted for more than 30 minutes or is temporarily interrupted, the printing template needs to be cleaned. It can continue to work after 1-2 trial printing. The solder paste attached to narrow space of the opening (≤0.4mm) and the opening of the stencil will gradually dry, which will degenerate the adhesive ability.
FH260 solder powder with excellent sphericity, uniform particle size, and low oxygen content is combined with halogen-free flux to produce FH-260P series solder paste. It is a high-temperature lead-free product developed for secondary reflow of power semiconductor and microelectronic packaging. The alloy is synthesized based on bismuth elements by adding reinforced micro/nanoparticles, successfully replacing high-lead solder paste, and meeting RoHS environmental protection standards.
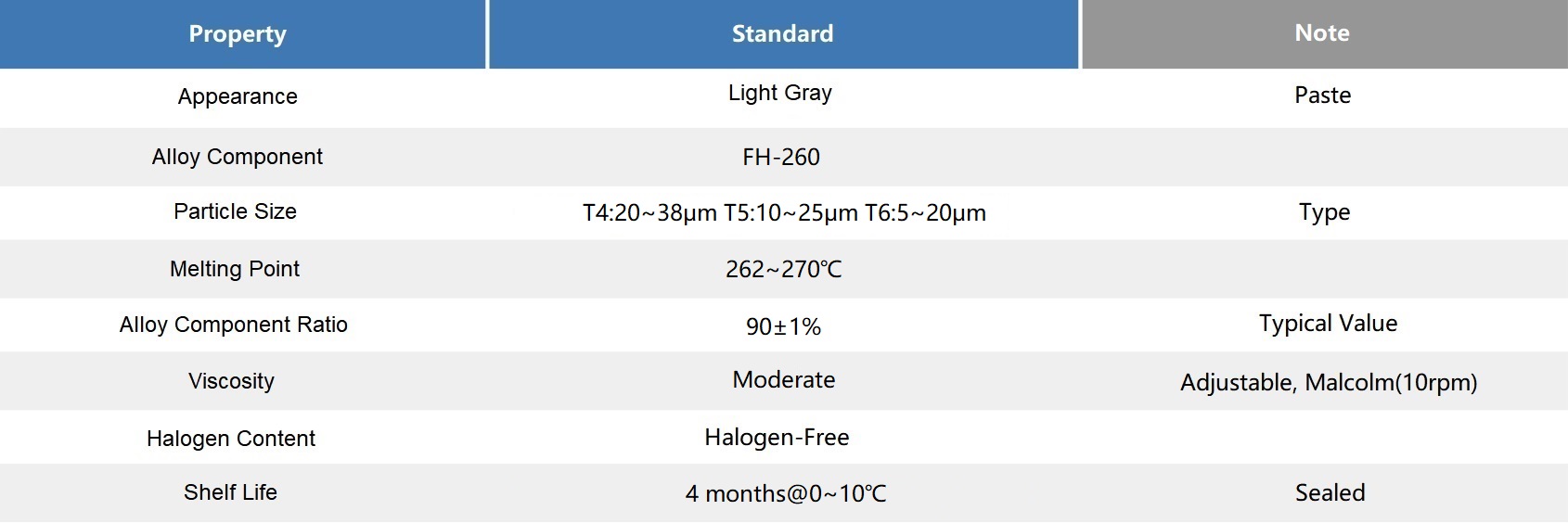

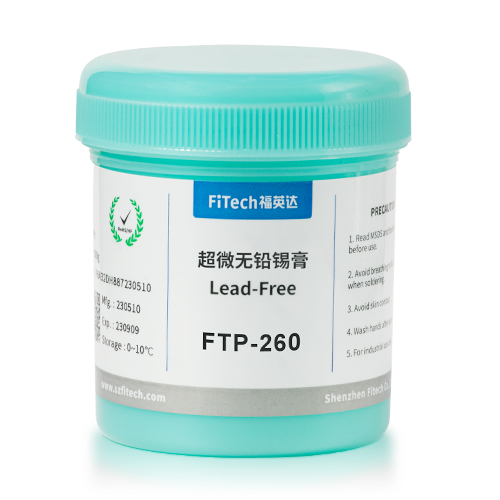
Warming Method: The sealed solder paste should rewarm to room temperature naturally; Rewarm no more than twice.
Warming Time: Rewarm 2 to 3 hours at room temperature. The actual time required to reach thermal equilibrium varies by vessel size.
Note: Do not open the bottle cap without sufficient rewarming or shorten the rewarming time by using heating equipment.
Operation Environment: The best operating temperature and humidity are 20-25°C and 40-60%RH, respectively. Reflow soldering in a nitrogen atmosphere is recommended.
SnSb10 alloy solder powder with excellent sphericity, uniform particle size, and low oxygen content is mixed with no-clean flux to produce FTP-901 series solder paste based on metallurgical method and chemical structure. FTP-901 has a superior adhesion effect before soldering. Solvent volatilizes very slightly during soldering. Moreover, FTP-901 has outstanding wettability, anti-slump, and residue reduction properties. It is developed to meet the marketing demand for heat-resistant microelectronic device assembly and precision soldering. The product has extraordinary heat resistance and heat dissipation abilities. It also improves soldering voiding and the strength and conductivity of intermetallic compounds.
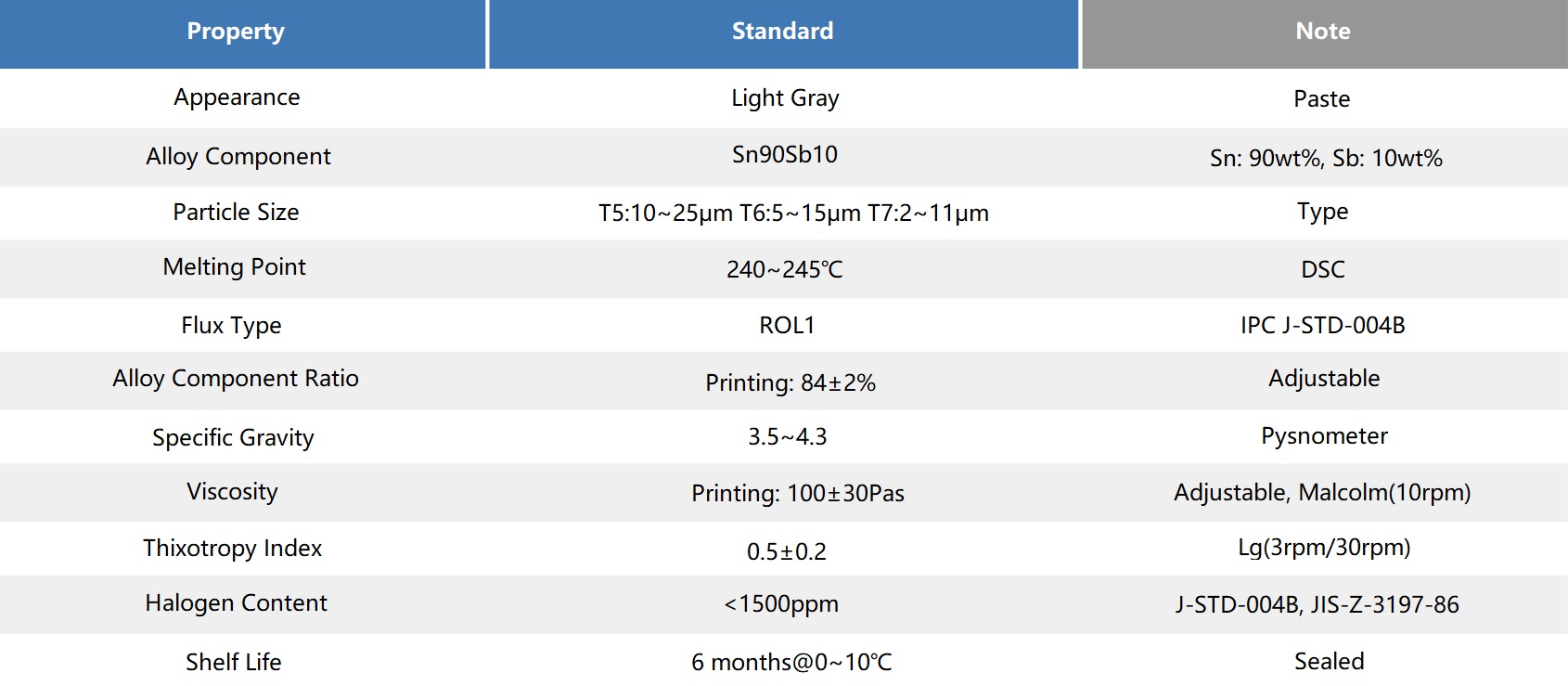
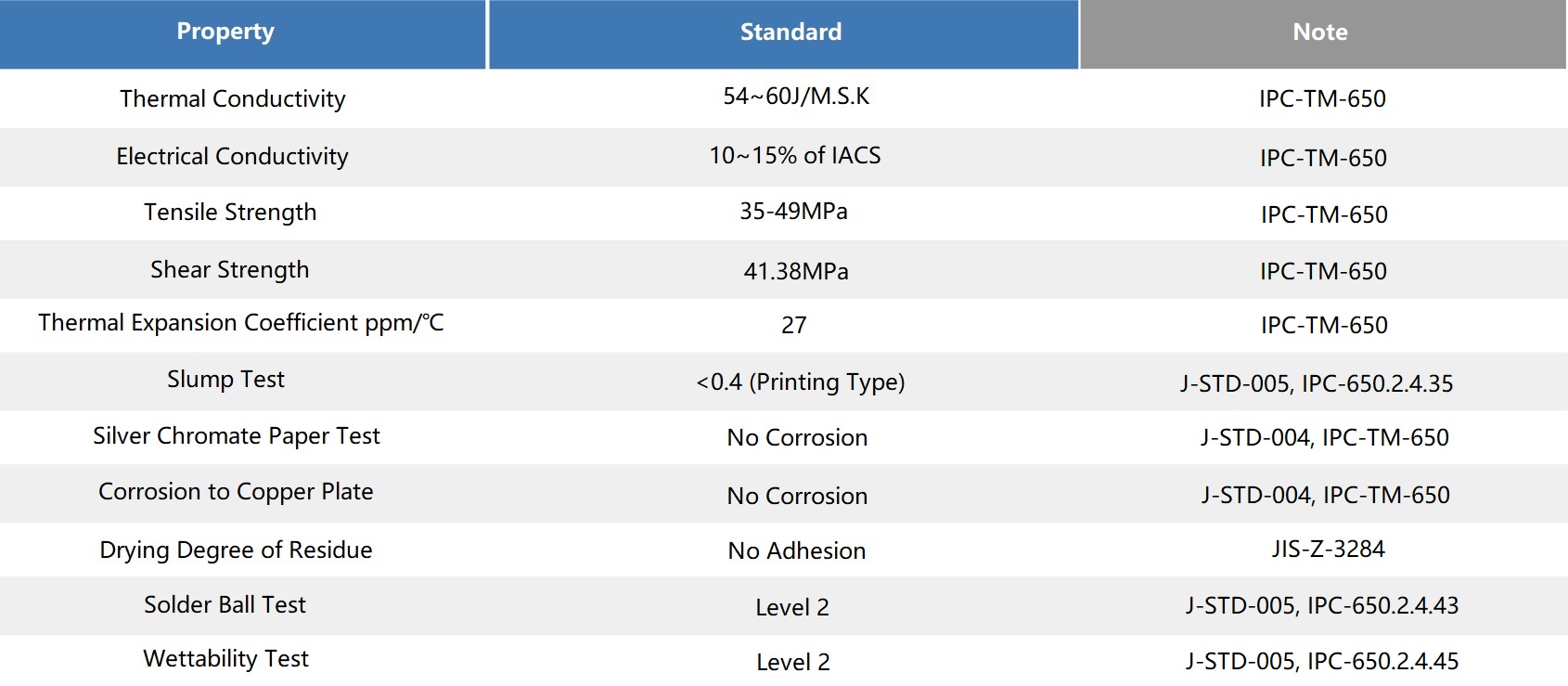
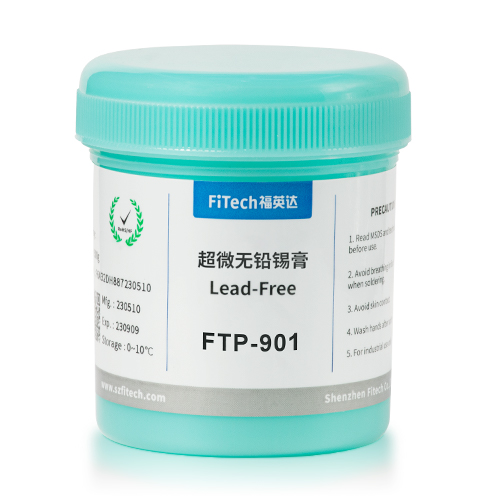
Warming Method: The sealed solder paste should rewarm to room temperature naturally; Rewarm no more than twice.
Warming Time: Return to warm for 2 to 3 hours at room temperature. The actual time required to reach thermal equilibrium varies by vessel size.
Note: Do not open the bottle cap without sufficient rewarming or shorten the rewarming time by using heating equipment.
Operating Environment: The best operating temperature and humidity are 20-25°C and 40-50%RH, respectively. Reflow soldering in a nitrogen atmosphere is recommended.