The Effect of Ultrasonic Treatment on SAC305 Solder Joint_Shenzhen Fitech
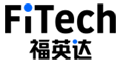
The Effect of Ultrasonic Treatment on SAC305 Solder Joint_Shenzhen Fitech
Applying ultrasonic treatment during the soldering process is a novel auxiliary method. By analyzing the morphology of the solder joint after soldering, it can be found that the application of ultrasonic assistance can affect the morphology of the intermetallic compound (IMC) layer at the interface of the solder joint, and the changes in IMC will have different effects on the mechanical properties of the solder joint.
1.1 Materials
Hu et al. used 10mm×50mm×2mm pure copper sheet and 10mm×10 mm×2mm pure copper sheet for the test. The sample was placed in a steel mold and subjected to ultrasonic treatment using an ultrasonic probe. To ensure a constant time for ultrasonic energy to propagate into the solder, the distance between the ultrasonic probe of each sample and the solder was the same. Therefore, the ultrasonic probe was fixed above the mold positioning groove.
Figure 1. Ultrasonic treatment of samples.
1.2 Soldering process
Hu et al. printed SAC305 solder paste evenly on the surface of the copper sheet and placed the assembled sample on a heating platform. The sample was heated with a heating rate of 25 ℃/min to 290℃ and then subjected to ultrasonic treatment. The sample was reflowed at a temperature of 290℃ for 10 minutes, and at the end of the reflow process, a 350W and 20kHz ultrasound treatment was applied to the sample.
From Figure 2, it can be seen that the shape of Cu6Sn5 is irregular, mostly in the form of rough scallops. When the ultrasonic treatment time is short, the thickness of Cu6Sn5 shows a decreasing trend, but the overall structure of Cu6Sn5 is similar to that of the solder sample without ultrasonic treatment. The difference is that due to the acoustic flow effect accelerating the diffusion of Cu atoms, free Cu atoms accumulate on the surface of the Cu6Sn5 layer in samples subjected to longer ultrasonic treatment time. Cu atoms react with the Sn atoms of the solder, resulting in an increase in thickness and more continuity of the Cu6Sn5 layer.
Figure 2. Microstructure of solder joints with different ultrasonic treatment times. (a) 0s; (b) 1s; (c) 5s; (d) 10s; (e) 15s; (f) 30s.
After 1s of ultrasonic treatment, the maximum shear strength of the solder joint slightly increased to 49.2Mpa. Compared with solder joints without ultrasonic treatment, the maximum shear strength of the solder joint increases by 20% when the ultrasonic time is increased to 5s. However, when the ultrasonic time is further increased, the strength of the solder joint actually decreases significantly. The change in shear strength can be understood by observing the fracture mode of the solder joint. The untreated solder joints exhibited fracture behavior near the substrate. However, as the ultrasound time gradually increased, fracture behavior was observed between the solder and IMC layer, indicating an improvement in the bonding force between the IMC layer and the substrate. However, further prolonging the ultrasonic time actually causes the solder joint fracture to occur again near the substrate.
Figure 3. Shear strength of solder joints at different ultrasonic treatment times.
Shenzhen Fitech has professional experience in solder paste research and production and can provide customers with high-quality solder paste for different soldering temperature needs. Fitech’s solder paste has stable viscosity, less soldering residue, and high solder joint strength. Welcome customers to have cooperation with us.
Hu, X.W., Xu, H., Chen, W.J. & Jiang, X.X. (2021). Effects of ultrasonic treatment on mechanical properties and microstructure evolution of the Cu/SAC305 solder joints. Journal of Manufacturing Processes, vol.64, pp.648-654.