Factors Affecting Flux Spatter_Shenzhen Fitech
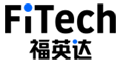
Factors Affecting Flux Spatter_Shenzhen Fitech
There is a problem with solder and flux spatter during reflow soldering, which can have a significant impact on the quality and reliability of electronic products. The residue of flux on PCB not only has chemical corrosiveness, but also some residues have insulation properties, which can affect the circuit test results. Flux spatter is influenced by various factors, including chemical composition, reflow profile, PCB roughness, surface finish, etc. This article mainly analyzes the effects of PCB roughness, chemical composition, and surface finish on flux splashing.
Flux spatter test
The spread of flux is influenced by surface tension. Due to the different surface tensions brought by smooth and rough surfaces, it can be expected that the roughness of the pad surface and its surroundings will affect the spread area of flux. Vesely et al. analyzed the factors affecting flux splashing by observing the splashing behavior of SAC305 solder paste (ROL0 and ROL1) on solder masks with different roughness (matt and bright) and copper pad surface treatments (HASL and ENIG).
Figure 1. Experimental samples. Matt solder mask and HASL surface finish (left); Bright solder mask and ENIG surface finish (right).
Figure 2. Experimental reflow profile.
Test result
Comparing the surface of the bright solder mask and the matt solder mask, it can be observed that there is a significant difference in the spread of the flux. Compared with the sample of the bright solder mask, the spread area of the flux in the test sample of the matt solder mask is significantly larger because of the smaller wetting angle of the matt solder mask. In addition, PCB with HASL surface finish will result in a higher spread area of flux.
Figure 3. Spread area of flux.
The amount of flux residue is directly related to the spread area of the flux. On surfaces with higher roughness, the area generated by sputtering is larger and the frequency of sputtering occurrence is higher. The amount of flux residue on the matt solder mask is approximately twice or more than the amount of residue on the bright solder mask. From Figure 4, it can also be observed that HASL and ENIG surface finishes do not cause significant differences in the amount of flux residue. In addition, the residue spatter of halogen-containing flux is more severe than that of halogen-free flux, because the oxide reduction effect caused by halides is stronger, resulting in a greater sputtering effect of flux. To reduce flux splashing, using halogen-free flux is a better choice.
Figure 4. Quantity of flux residues.
Fitech’s solder paste
Shenzhen Fitech has industry-leading research and production capabilities in flux research and development. Fitech can provide customers with halogen-free and halogen-containing flux products with low residue and excellent activity. In addition, Fitech can also provide high-quality lead-free solder paste products, including SAC305, SnBi57.6Ag0.4 solder paste, etc. Welcome customers to have in-depth cooperation with us.
Vesely, P., Busek, D., Krammer, O. & Dusek, K. (2020). Analysis of no-clean flux spatter during the soldering process. Journal of Materials Processing Technology, vol.275.