Soldering Performance of Epoxy SAC305 Solder Paste_Shenzhen Fitech
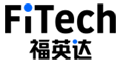
Soldering Performance of Epoxy SAC305 Solder Paste_Shenzhen Fitech
The safety performance of consumer electronics has been highly valued by the industry, especially in automobiles and medical devices. Facing different environmental temperatures of electronic products, the reliability of packaging needs to meet the requirements. With the increasing demand for packaging reliability, packaging material developers have proposed various methods to improve solder joint reliability, such as adding nano-reinforced particles to solder. Another way is to add a curable epoxy resin to the flux. After the epoxy resin is cured, it forms a protection for solder joints and improves soldering reliability.
With the increasing recognition of epoxy-based solder paste from industry manufacturers, many solder manufacturers have increased their research and development of epoxy solder paste. Sharma et al. prepared a no-clean solder paste by mixing T4 SAC305 powder with epoxy-doping flux. They conducted reliability tests on epoxy SAC305 solder paste and compared it with normal SAC305 solder paste.
Reliability Tests
Epoxy SAC305 solder paste was applied to the PCB pad, and then the automotive 1608 resistors were placed onto the solder paste. After reflow soldering, the epoxy resin solidified and formed an insulation resistance layer around the solder joints. The reliability tests included a thermal cycle test, shear force test, and surface insulation resistance (SIR) test.
Figure 1. Test sample.
Thermal cycling test
The temperature of the thermal cycle test was controlled between -40°C and 125°C. Both high and low temperatures were maintained for 30 minutes and continued for 1000 aging cycles. From the figure, it can be seen that the after-reflowed solder joints are wrapped in epoxy resin. As the number of thermal cycles increases, the epoxy resin layer gradually extrudes outward, resulting in a decrease in the encapsulation of the solder joint. This is because the epoxy resin is imperfectly cured. For epoxy SAC305 solder paste, the thickness of Cu6Sn5 continuously increases with the increase of thermal cycles. However, compared to ordinary SAC305, the growth rate of Cu6Sn5 thickness is slower, which can be attributed to the absorption and outward release of stress in epoxy solder paste.
Figure 2. Appearance of solder joints after thermal cycling test.
Figure 3. Growth of Cu6Sn5 in epoxy solder paste and ordinary solder paste.
Shear force test
For shear force testing, the loading force was controlled at 50N and the shear speed was 200μm/s. The results show that the shear forces of epoxy SAC305 solder joints decrease with increasing aging time. However, due to the slow growth rate of IMC, the decrease in the shear force of solder joints was relatively small. Overall, the shear strength of epoxy SAC305 solder joints is higher than that of ordinary SAC305 solder joints.
Figure 4. Shear force test results.
Surface insulation resistance test
The surface insulation resistance test was conducted on a standard comb board. After reflow soldering, the solder paste was tested at high humidity (90-95% RH) and 28-32°C for 168h. By applying a potential of 100V at both ends of the comb structure, the corresponding resistance can be measured. It was found that the average SIR of the resin insulation layer of the solder joint was 2.58×10^13 Ω, higher than the SIR of ordinary SAC305. This indicates that ordinary SAC305 solder paste has relatively more flux residue, making solder joints more susceptible to corrosion, while epoxy resin can protect solder joints to a greater extent, reducing solder joint failure caused by moisture.
Fitech's solder paste
In order to meet the market demand for highly reliable solder joints, Shenzhen Fitech has independently developed epoxy-based solder paste products. The solder joints have high strength and excellent conductivity, and the cured epoxy resin can effectively protect the solder joints from external forces and corrosion effects.
Reference
Sharma, A., Jang, Y.J., Kim, J.B. & Jung, J.P. (2017). Thermal cycling, shear and insulating characteristics of epoxy embedded Sn-3.0Ag-0.5Cu (SAC305) solder paste for automotive applications. Journal of Alloys and Compounds, vol.704, pp. 795-803.