The Wettability of SAC305 Solder with SiC Doping_Shenzhen Fitech
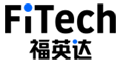
The Wettability of SAC305 Solder with SiC Doping_Shenzhen Fitech
Intermetallic compounds (IMCs) of SAC305 traditional solder paste grow quickly during soldering, which can easily form thicker IMC layers and affect the reliability of the solder joints. It can be known that SiC is a high melting point ceramic material. By adding a small amount of micro/nano SiC particles into SAC305, SiC stays in the solder matrix after the solder melts and solidifies, which can refine the solder joint structure and act as a barrier for metal atom diffusion, resulting in a significant slowdown in the growth rate of the IMC layer at the interface of the solder joint. In addition, in recent years, many researchers have found that ceramic particles can improve the wettability of solder on the substrate, thereby improving the microstructure of solder joints.
Preparation and wettability test of SAC305-SiC solder
Pal et al. added SiC particles with an average diameter of 2μm into the SAC305 solder for the synthesis of composite solder. SiC and SAC305 powders were mixed in high-energy ball milling for about 1h. SiC and SAC305 powders were uniaxially compacted in a mold (cold pressed at 200Mpa at room temperature) to form cylindrical rods with a diameter of 3mm. Then, the sample was placed in a furnace for melting to produce SAC305-1.0%SiC composite solder.
Figure 1. Preparation steps of SAC305-SiC solder.
Pal et al. tested the microstructure development and wettability changes of SAC305-1.0% SiC composite solder on a clean Cu substrate at different reflow temperatures from 230°C to 290°C. The sample is kept under reflow for about 60 minutes, during which it reaches the equilibrium condition of wettability.
Results
The IMC structure
Figure 2 shows the microstructure of SAC305-1.0% SiC/Cu surface after the reflow process at different reflow temperatures. After adding 1.0wt%SiC, Cu6Sn5, and Ag3Sn IMCs appeared in the Sn solder matrix but near the interface. The layer in contact with Sn is Cu6Sn5, while the Cu3Sn layer is located between Cu6Sn5 and Cu. As the reflow temperature increases from 230°C to 290°C, the Cu6Sn5 IMC layer in the liquid/solid reaction slows down. The Cu6Sn5 layer decreases with the growth of the Cu3Sn layer, and the Cu3Sn layer increases with the increase in temperature. Non-wettable SiC is usually transferred from the molten solder. The morphology of interface IMCs indicates that pores are formed during the reflow process due to the segregation of SiC particles.
Figure 2. IMC situation of SAC305-1%SiC at different reflux temperatures.
Wettability
When the reflow temperature is 270°C, the maximum relative spread area of SAC305-1.0%SiC solder is 76%, which is about 24% larger than the maximum relative spread area at 230°C. As the reflow temperature rises to 290°C, the maximum relative spread decreases to around 68%. Therefore, it can be known that the spread area of solder first increases with the increase of temperature, and as the temperature continuously increases, the spread area significantly decreases.
Figure 3. Relationship between SAC305-1.0%SiC spread area and reflow temperature.
At a reflow temperature of 230°C, the contact angle of SAC305-1.0%SiC solder joints is relatively large, indicating poor wettability of the composite solder. As the temperature increases, the contact angle of the solder joint begins to decrease, and the surface wettability improves. When the reflow temperature further increases to 290℃, the contact angle begins to increase. These results confirm that at specific reflow temperatures, improving the wettability of the solder substrate can be achieved by increasing SiC particles.
Table 1. Contact angles of SAC305-1.0%SiC at different reflow temperatures.
Reference
Pal, M.K, Gergely, G., Koncz-Hoevath, D. & Gacsi, Z. (2021). Investigation of microstructure and wetting behavior of Sn–3.0Ag–0.5Cu (SAC305) lead-free solder with additions of 1.0wt%SiC on copper substrate. Intermetallics, vol.128.