The Prospect of SAC305 Nano-Solder Paste and Microwave Hybrid Heating_Shenzhen Fitech
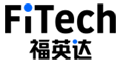
The Prospect of SAC305 Nano-Solder Paste and Microwave Hybrid Heating_Shenzhen Fitech
SAC305 has been widely used as a substitute for lead solder on the market. The reliability of SAC305 has always been a concern in the industry. It is known that the formation of intermetallic compounds (IMCs) layer between SAC305 and substrate is an important factor significantly affecting the reliability of solder joints. The methods to reduce the formation of IMC layers include using rapid heating and shortening the holding time during reflow soldering. In addition, research has found that using microwave energy can achieve faster and more uniform heating than reflow soldering, which is called microwave hybrid heating technology (MHH). Compared with traditional reflow soldering, solder joints produced using MHH technology exhibit higher strength and better corrosion resistance. In addition, to meet some low-temperature soldering needs, using nanoscale solder materials will be an alternative to traditional low-temperature solders. Therefore, SAC305 nano-solder has also received attention.
Preparation and soldering test of SAC305 nano-solder paste
Zhang et al. synthesized SAC305 nano-particles using the chemical reduction method. Firstly, they weighed the Sn source (SnSO4), Ag source (AgNO3), and Cu source (CuSO4·5H2O) as precursors, as well as the reaction solvent C4H10O3 and PVP surfactant. Secondly, the materials were mixed using a magnetic stirrer. After mixing, they washed the solution several times with water and anhydrous ethanol, centrifuged using a high-speed centrifuge, and removed the supernatant. Detergent was added to the precipitate. The sludge was sonicated and mixed. Centrifugation was repeated until the solution cleared. After washing, the obtained nanoparticles were placed under vacuum drying at 25°C to obtain the product. Finally, the ground SAC305 nanoparticles were mixed with ALPHA OM338PT flux in a 6:1 ratio to obtain the solder.
Zhang et al. applied nano-solder paste onto Cu with oxide film removed through steel mesh printing and placed Cu in a tight mold. The experimental components are stacked in the microwave oven in the order of insulation, graphite cavity, and base. The sample was cooled at the air to room temperature after soldering.
Figure 1. Schematic diagram of MHH process.
Preparation and soldering test of SAC305 nano-solder paste
The experimental results
The effect of surfactants on the particle size of SAC305 nanoparticles is shown in Figure 2. The size distribution of SAC305 nanoparticles prepared with different surfactant contents varies. When the amount of PVP surfactant is small, the average particle size of SAC304 nanoparticles is larger. After increasing the amount of surfactant to 0.9g, the average particle size of SAC304 nanoparticles is the smallest (77.42nm), and the mass ratio of surfactant to nanoparticles is 90%. As the amount of surfactant is further increased, the particle size distribution tends to stabilize because an appropriate increase in surfactants can reduce surface tension and promote particle separation. Surfactants effectively coat nanoparticles and prevent aggregation by forming stable complexes with atoms through coordination.
Figure 2. The effect of surfactant amount on the particle size distribution of nanoparticles. (a) 0.15g; (b) 0.3g; (c) 0.6g; (d) 0.96g; (e) 1.2g.
The effect of MHH on the strength of solder joints
For the MHH process, under an exposure time of 165s, the shear strength of solder joints made of nano SAC305 solder paste is 27MPa. As the exposure time increases, the shear strength of the solder joint first increases and then decreases. When the exposure time reaches 195s, the maximum shear strength is 44.8 MPa. Further increasing the exposure time has an adverse effect on shear strength. In addition, the MHH process can provide good thermal shock reliability for solder joints. After 1200 thermal shock cycles, the shear strength decreased by 24.4% and the fracture mode remained ductile fracture.
Figure 3. Relationship between shear strength and thermal shock cycles of SAC305 nano-solder paste.
Reference
Zhang, S., Zhang, S.Y., Zhou, H.Z., Paik, K.W., Ding, T.R., Long, W.M., Zhong, S.J. & He, P. (2023). Preparation and characterization of Sn-3.0Ag-0.5Cu nano-solder paste and assessment of the reliability of joints fabricated by microwave hybrid heating. Materials Characterization, vol.207.