Relationship between Laser Soldering Reflectivity and Solder_Shenzhen Fitech
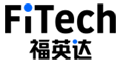
Relationship between Laser Soldering Reflectivity and Solder_Shenzhen Fitech
As surface assembly technology develops towards high density and small size, the traditional reflow soldering process may cause damage to heat-sensitive devices, so a process that can heat and solder devices in specific areas is needed. Laser soldering is a new type of soldering process. This technology can localize non-contact heating and has a short heating time to form reliable solder joints. However, there is still a disturbing phenomenon during laser soldering, which is the random burning of heat-sensitive components around the solder joints. This situation is mainly caused by the laser reflectivity (LR) of the pad and solder ball during the laser jet solder ball bonding process. Therefore, it is necessary to understand the relationship between LR and solder.
Experimental design
Zhao et al. (2022) used an FR4 copper-plated plate and a green oil plate with a size of 60×60. Before the experiment, the surface of the plate was cleaned with absolute alcohol. The solder used was WTO-LF2000 no-clean SAC305 solder paste. Zhao et al. used low laser power for laser soldering experiments.
Experimental results
When laser power is used to irradiate solder, the interaction between the laser and the melting and diffusion of SAC305 solder paste is likely to form a reflection and produce a dazzling white light. The large amount of thermal radiation formed will burn the surrounding components.
Figure 1. (a) LR and (b) component burnout.
In order to allow the low-power laser to melt the SAC305 solder paste, a ceramic heating plate is used to assist in solder melting. The ceramic heating plate first heats the solder paste to 200°C, and then the laser irradiates and gradually melts the solder paste. LR during laser soldering can be divided into five stages. The initial phase (0-0.3s) is characterized by low LR and rapid heating of the solder. During this stage, the LR slowly increases from 23% to 28%, the solder absorbs a lot of heat, and the temperature quickly rises from 200°C to 249°C. The second stage (0.3-0.4s) is the rapid rise moment of LR and the temperature is maintained at 247-249°C. The third stage (0.4-0.7s) is characterized by a decrease in LR. LR increases again in the fourth stage (0.7-2.3s). Due to the inertial effect, the temperature first rises to 257°C and drops to 220°C due to the increasing LR. The LR remains stable in the final stage (2.3-5.0s), and the temperature is around 225°C.
Figure 2. LR and temperature changes during laser soldering.
Figure 3. Solder wetting and LR changes.
In the initial stage, the laser is reflected on the solder paste and is absorbed by multiple reflections from the SAC305 powder. LR is determined by the solder paste itself. As reflection continues, some areas melt, causing the laser to be reflected by the liquid, and the LR slowly increases. As the degree of solder melting increases, LR increases significantly. However, due to the short duration, it will not cause damage to components. In the third stage, heat is conducted downward due to the temperature difference between the upper high-temperature liquid and the lower unmelted powder. At the same time, the molten solder in the upper layer needs to absorb more laser energy to increase or maintain the temperature, resulting in a rapid decrease in LR. In the fourth stage, more and more powder melts into liquid, the effects of temperature difference and heat conduction decrease, and laser reflection increases. However, the laser is reflected radially by the sphere and will not directly damage the components. Finally, since the solder is completely melted, the heat exchange between the solder and the external environment reaches equilibrium, so the laser reflection stably remains at a high level, and most of the laser is concentratedly reflected to the surrounding components and causes damage.
Fitech's solder
Fitech is committed to the R&D and sales of electronic-grade solder materials and can provide customers with ultra-fine solder paste and powder (T6 and above). Fitech’s products include low-temperature and high-temperature solder, which has concentrated particle size, low oxygen content, less residue, and high reliability. Welcome to contact us for more information.
Reference
Zhao, S.N., Tan, Z.D., Wang, H.Y. & Gao, M. (2022). Effects of spreading behaviors on dynamic reflectivity in laser soldering.Optics & Laser Technology, vol.155.