Solder Joint Improvement by Flux Doped with Cu-Modified Carbon Nanotubes _Fitech Solder Paste
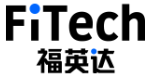
Solder Joint Improvement by Flux Doped with Cu-Modified Carbon Nanotubes
Flux is one of the components of solder paste, which plays the role of removing oxides and improving the wettability of solder paste. However, even if different types of fluxes are used, the continuous growth of intermetallic compounds (IMCs) will still occur during soldering and aging. The excessive IMC growth and grain coarsening will seriously damage the mechanical strength of solder joints, which has always troubled the electronic packaging industry. Therefore, it is very important to find a way to slow down the formation of IMCs. In recent years, increasing number of R&D personnel have realized that doping carbon nanotubes into the flux can enhance the solder joints, and is expected to meet the increasingly stringent requirements for highly reliable solder joints.
1. Flux doped Cu modified carbon nanotubes (Cu-CNTs)
Wang et al. proposed a nanotube doping scheme that carboxylated Cu-CNTs can be added into SAC305 flux to reduce IMCs. Compared with pure flux, the flux doped with Cu-CNTs can delay the growth of Cu6Sn5 IMC and inhibit the grain coarsening of IMC. Besides, Wang et al. also applied ultrasonic vibration when conducting reflow to further reduce the thickness of IMC.
2. Reflow and aging test
Wang et al. applied the fluxes doped with Cu-CNTs to one side of the copper sheets, and then SAC305 solder balls were placed into the fluxes. The copper sheets were reflowed on the heat stage at 250℃. When the solder balls melted, the ultrasonic generator acted on the other side of the copper sheets at a frequency of 20kHz for 5s.
Figure 1. Schematic diagram of reflow test.
After reflow, the copper sheets were isothermal aged for 360h at 150℃. The microstructures of the solder joints were observed after the aging test.
3. IMC thickness and grain size
Normally, the interface IMC layer gradually thicken with the increase of aging time. After reflow, the interface IMC is mainly Cu6Sn5. As the aging time of solder joints increases, IMC is generated mainly in the form of Cu3Sn. It can be seen from Figure 2 that the Cu-CNTs-doped fluxes make the solder joints develop a thinner interface IMC layer compared with the solder joint using pure fluxes, which means that introducing Cu-CNTs can hinder the growth of IMC layers. When the amount of Cu-CNTs is 0.1wt%, the thickness of the IMC layer generated reaches the smallest value, representing that 0.1wt% Cu-CNTs doping can most effectively inhibit the growth of IMC layers. However, if more Cu-CNTs is added to the flux, it is easy to cause the aggregation of Cu-CNTs, which weakens the ability to inhibit the diffusion of Sn and Cu atoms.
Figure 2. Effect of Cu-CNTs doping amount on interficial IMC thickness.
The IMC grains become coarser with aging, and the flux doped with Cu-CNTs for the solder joints can produce more refined IMC grains. In addition, Cu-CNTs are widely distributed inside the solder joint, which can hinder the transfer of shear force to a certain extent, thus ensuring better mechanical strength of the solder joint.
Figure 3. Effect of Cu-CNTs doping amount on interficial IMC grain size.
4. Highly reliable solder paste products
Shenzhen Fitech has two decades of solder paste production experience. Fitech’s ultra-fine solder paste products (T6 and above) have stable viscosity, excellent tackiness and outstanding wettability, which have been verified and adopted by many clients. Welcome to contact us for more product information.
5. Reference
Wang, H.Z., Hu, X.W. & Li, Y.L. (2021). Interfacial reaction and shear strength of ultrasonically-assisted Sn-Ag-Cu solder joint using composite flux. Journal of Manufacturing Processes, vol.62, pp.291-301.