Fitech’s Solder Pastes for Automotive Electronic: Wire Bonding Reliability of Automotive MEMS Sensors
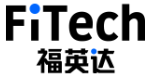
Fitech’s Solder Pastes for Automotive Electronic: Wire Bonding Reliability of Automotive MEMS Sensors
Click to view "Fitech’s Automotive Electronic Solder Paste"
Micro electro-mechanical systems (MEMS) have been used for decades in the field and are still one of the ubiquitous electronic components. MEMS sensors play an essential role in the automotive industry and can be used to measure position, pressure, temperature, speed, etc. The high reliability of the sensor not only improves the automotive performance but also ensures the safety of the driver and passengers. MEMS chips often use gold wires to bond with the pads. The gold wires can realize the electrical connection and signal transmission. MEMS chips need to be encapsulated to avoid environmental interference. Encapsulation is usually made of plastic, which has a low cost and can reduce packaging costs.
MEMS wire bonding has several failure modes and mechanisms, mainly related to thermal and electrical effects. For example, intermetallic compounds formed during reflow soldering due to thermal action and atomic diffusion cause solder joint embrittlement, and Joule heat generated during sensor operation can cause electrical fatigue. What’s more, there is thermal fatigue caused by thermal stress induced during use. To test the reliability of MEMS devices, Zhang et al. studied the thermal failure behavior of gold wire bonding solder joints of automotive MEMS pressure sensors in thermal cycle tests. The thermal cycle temperature is controlled at − 40 °C-150 °C. The number of test samples is 25, each containing 4 gold wires.
Figure 1. The testing automotive MEMS pressure sensor.
Figure 2. Thermal cycle test temperature profile.
Test Result
The number of thermal cycle test cycles was set at 1600 by Zhang et al. After every 200 thermal cycle tests, all MEMS pressure sensor samples were taken out, and the resistance of solder joints was measured. The increase in resistance indicates that the conductivity of the solder joint decreases. After 1600 thermal cycles, 7 of the 25 samples tested had the same phenomenon of solder joint resistance increase. Thermal stress is the main reason that affects the resistance change of MEMS sensors. Thermal stress will continuously accumulate and deteriorate the reliability of solder joints, resulting in increased resistance.
Thermal stress affects both the resistance and the mechanical reliability of solder joints. Zhang et al. mapped the wire bonding state of the MEMS pressure sensor after thermal cycling through CT scanning. A total of 8 solder joints of 4 gold wires were selected for observation. It can be seen that 3 gold wires and pads remained connected. However, the 5th solder joint was obviously stripped off. In addition, loose wires affected by thermal stress were found at the 7th and 8th solder joints, and the firmness of the solder joints decreased.
Figure 3. CT scan of the MEMS pressure sensor after 1600 thermal cycles.
It can be seen from the thermal cycle test that the automotive MEMS pressure sensors used in the test were difficult to ensure good bonding strength after 1600 cycles. It can be considered that thermal stress is an important cause of solder joint failure. The difference in thermal expansion coefficients between the gold wire and bonding pad made them deform at varying degrees after temperature change, reducing the connection firmness of solder joints.
For automotive electronic soldering materials, Shenzhen Fitech can provide excellent solder pastes products that apply to scenarios with different soldering temperature requirements. The solder joint strength can be guaranteed regarding various clients’ requirements.