Laser Soldering Reliability - Fitech’s Laser Solder Paste
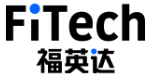
Laser Soldering Reliability - Fitech’s Laser Solder Paste
After years of practice, reflow soldering is now a fairly mature soft soldering process. The reflow time only takes a few minutes. Is there a faster soldering process? The answer is yes. The application of laser technology is very early and wide, but it is relatively late in soft soldering. Laser soldering generates heat energy by emitting a laser beam, which can melt the solder paste/solder ball and finish soldering in a few seconds. Laser soldering can be used in low-temperature and high-temperature soldering occasions, with the advantages of local heating, non-contact and short working time. Laser heating can accomplish the task of point-to-point soldering on small pads and has a broad application prospect in electronic equipment with high package density and chip miniaturization.
Laser soldering test
The reliability of laser soldering has always been a topic of discussion in the industry. It is necessary to constantly explore the solder material formulations and laser soldering process to find the appropriate parameters. For this reason, Jeong et al. conducted a reliability test on laser soldering. They selected Sn42Bi58 BGA solder balls and ENEPIG-treated pads as test materials. The testing laser power includes 130W, 150W, and 170W, and the soldering duration is 2s and 4s.
Figure 1. Schematic diagram of test pad and laser soldering process.
Laser solder joint microstructure
Effective soldering is achieved through metallurgical bonding, mainly through the interface reaction between the solders and the pads, forming specific IMCs. As can be seen from Figure 2, when the laser power was low (130W), the IMC type generated on the soldering surface was plate type (Pb, Au) Sn4. When the soldering condition changed to 150W (2s), IMC was still (Pb, Au) Sn4. However, if soldering at 150W for 4s, the IMC changed, and (Cu, Ni) 6Sn5 appeared. In addition, some Ni was consumed by the reaction, and a P-rich Ni layer formed. P rich Ni layer was also found after laser soldering at 170W (4s). At high energy, Au and Pd layers completely dissolved into solder and led to (Pb, Au) Sn4.
Figure 2. SEM images of the soldering spot after laser soldering. (a, b) 130W, 4s; (c, d) 150W, 2s; (e, f) 150W, 4s; (g, h) 170W, 2s; (i, j) 170W, 4s.
After aging at 110 ℃ for 100 hours, P-rich Ni layers could be observed in all samples, and (Cu, Ni) 3Sn formed under the P-rich Ni layers. For 130W(4s) and 170W(2s) conditions, (Pd, Au)Sn4 spalled at the interface. For the samples tested under the condition of high laser energy 170W (4s), the IMC thickness after aging was greater than that of the samples tested under other conditions, and a part of (Cu, Ni)6Sn5 is converted into (Cu, Ni)3Sn. Bi-segregation also occurred. Bi segregation was due to the low solubility of supersaturated Bi in (Cu, Ni)3Sn, resulting in Bi precipitation.
When the aging time was further extended to 2000 hours, more (Cu, Ni) 3Sn grew in all laser soldering conditions. Besides, Bi segregation and voids began to appear in the solder joints with the soldering condition of 150W (4s), which weakened the reliability of solder joints.
Figure 3. SEM images of solder joints aged at 110 ℃ for 100 hours. (a, b) 130W, 4s; (c, d) 150W, 2s; (e, f) 150W, 4s; (g, h) 170W, 2s; (i, j) 170W, 4s。
Figure 4. SEM images of solder joints aged at 110 ℃ for 2000 hours. (a) 130W, 4s; (b) 150W, 2s; (c) 150W, 4s; (d) 170W, 2s; (e) 170W, 4s。
Shear strength
Shear strength is directly related to aging time. With the increase of aging time, the fracture mode of the laser solder joint changed from ductile fracture to brittle fracture. During aging, brittle IMC grew excessively, IMC layer thickened. Bi-segregation and voids led to the decline of shear strength. The trend of shear strength change of all test samples during aging was similar. The shear strength of 150W (4s) solder joints decreased significantly after 500 hours of aging. For the soldering condition of 170W (4s), the strength of solder joints decreased significantly after 250 hours. The samples with 130W (4s) and 170W (2s) had lower shear strength in the early aging period. However, after aging for 2000 hours, the solder strength was superior to others. Jeong considered that 170W (2s) is the best laser soldering condition, at which the shear strength was excellent after a long time of aging, and the strength decline rate was much smaller than the condition of 130W(4s) during 1000-2000 hours of aging.
Figure 5. Shear strength change during aging.
Shenzhen Fitech has the production capacity of laser solder pastes that have good tackiness and excellent soldering spatter resistance. Welcome to contact us.
Reference
Jeong, M.S., Lee, D.H., Kim, H.T. & Yoon, J.W. (2022). “Reliability of laser soldering using low melting temperature eutectic Sn-Bi solder and electroless Ni-electroless Pd-immersion Au-finished Cu pad”, Material Characterization, vol.194.