Insufficient Volume Problem of Printing Solder Paste - Shenzhen Fitech
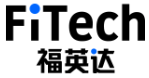
Insufficient Volume Problem of Printing Solder Paste - Shenzhen Fitech
The problem of insufficient solder in the solder paste printing process is mainly attributed to the following reasons:
(1) Inappropriate stencil thickness
For square and rectangular apertures, the aperture area can be simply calculated by length times width (L x W).
Hole wall area=2T(L+W)
For circular aperture structure:LW/(2T(L+W))
In process of solder paste printing, four forces are mainly considered, including the downward pull of the PCB pad on solder paste, the gravity of solder paste, the tackiness of the aperture wall to solder paste, and the tackiness of residual solder paste on the stencil to solder paste in apertures. The force that plays a leading role in printing quality is the downward pull of the PCB pad on the solder paste and the gravity of the solder paste. The sum of these two forces must be greater than the tackiness of the aperture wall to the solder paste to ensure smooth solder release. The greater the stencil thickness, the greater the aperture wall tackiness to the solder paste, inhibiting solder release.
The mismatch between the minimum aperture and the stencil thickness will lead to the problem of insufficient solder. If the minimum aperture length is more than 5 times the aperture width, the aperture width needs to be more than 1.5 times the thickness (L>5W, W/T>1.5). When the aperture length is not more than 5 times the width, the aperture area should be more than 0.66 times the aperture wall area (L<5W, aperture area/wall area>0.66).
(2) Inappropriate solder paste alloy powder size
Solder paste printing process needs to follow the "five ball rule". The shortest side of the square/rectangular aperture needs to accommodate at least five solder particles (the upper limit of the particle size is the benchmark). If the width of the rectangular aperture is 0.2mm, T4 solder powder (20-38 μm) should be used. If using circular apertures, the aperture diameter should be 8 times the size of solder particles. If the solder particles are large, it is easy for the powder to get stuck in the apertures, resulting in a poor solder release effect.
Calculation: 38 μ m x 5 = 190 μ m = 0.19mm<0.2mm
(3) High roughness of aperture wall
Stencil manufacturing types include etching, laser cutting, and electroforming. The stencil made by the etching method has a protrusion in the middle, which is not conducive to solder release. Laser-cutting stencil has large aperture wall roughness, and there are burrs on the walls, which is easy to lead to the problem of solder insufficient. The aperture wall roughness can be observed by a stereo microscope. The electroformed stencil has the smoothest walls, and the aperture is in the inverted trapezoidal shape, which significantly improves the solder release effect.
(4) Improper stencil surface tension
Insufficient tension will easily cause the stencil to fall during solder releasing, which will affect the release property of solder paste and lead to low solder paste volume on PCBs.
(5) High/Low squeegee pressure
The influence of excessive squeegee pressure is reflected in insufficient solder paste thickness. During printing, the squeegee with low rigidity is deformed due to the large pressure on the unit length, digging out the solder paste from the large apertures. As a result, the middle of the solder paste points collapses, forming a saddle-like structure (Figure 2). The printing quality can be improved by adopting stepped squeegees or maintaining an appropriate printing pressure. On the contrary, small squeegee pressure will lead to insufficient solder.
(6) Deterioration of printing solder paste
After the solder paste is placed on the stencil for a long time, the viscosity will become larger, and caking will occur. The solder paste with high viscosity will stick to the squeegee, resulting in insufficient solder paste during printing. The viscosity change of solder paste should be as small as possible to meet the requirements of longer printing time and on-board time. In addition, when the manufacturing output is low, the amount of onboard solder paste should be reduced to avoid long-time exposure. Multiple solder paste recycling is not conducive to maintaining the printing quality. Generally, it is not recommended to recycle more than twice. The frequency of temperature recovery will lead to the degradation of solder performance. What’s more, it should be noted that the solder paste on both sides of the squeegee should be timely collected into the solder pot and fully stirred for 2-5 minutes before reuse.
(7) High printing/solder release rate
The shear thinning property of solder paste makes it closer to the liquid state when the shear rate is large. If the squeegee movement is too fast, the aperture filling effect of solder paste is poor, forming a roof-like solder point. The large solder release rate can make the solder stick to the aperture walls, which is detrimental to the solder release.
Shenzhen Fitech is a professional manufacturer of ultra-fine solder pastes, which can produce printing solder paste with different viscosity to meet different printing requirements of the customers. Fitech’s ultra-fine printing solder pastes have stable viscosity, excellent wettability, and long on-board time. Welcome to contact us for more product information.