SMT Solder Paste Printing Process - Automatic Solder Paste Feeding
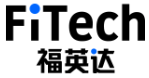
SMT Solder Paste Printing Process - Automatic Solder Paste Feeding
The solder paste printing process is a section of the SMD assembly process that uses metal stencils to coat solder paste on the PCB pads. After reflow soldering, solder pastes turn to solder joints to connect the SMDs and PCBs. The printing process is completed by an automatic printing machine. The squeegee of a printing machine moves horizontally to print the solder paste into the stencil apertures. As the printing process consumes a lot of solder paste, it needs to be supplemented frequently to ensure continuous printing. The automatic solder paste feeding device of the printing machine can add solder paste without manpower.
Figure 1. Automatic solder paste feeding unit.
There are two kinds of solder paste automatic feeding methods. The first type requires automatic detection and monitoring with the aid of height sensors, while the second type is to achieve timing and quantitative addition according to the change of solder paste volume on the stencils. The automatic addition amount of solder paste needs to be controlled in combination with the stencil size, product yield, PCB size, and other relevant data. At the same time, it is necessary to evaluate whether the automatic addition system is applicable. The evaluation criteria include the minimum volume of solder paste added in a single time, the occupation time, the system stability and continuity, and the residual solder paste volume.
(1) Height sensor monitoring: the height sensor is installed in the automatic solder paste feeding device to measure the height and width of the solder paste strip formed by the solder paste rolling during the printing operation. This method has high accuracy because the sensor can precisely measure the tiny change in solder paste size, which can ensure a sufficient volume of solder paste on the printing zone.
(2) Timing and quantitative feeding: It requires accurate solder paste consumption calculation. The operator needs to calculate the amount of solder paste required on each PCB and set the data to the printing machine. Then calculate the amount of solder paste automatically added according to the total PCB printing quantity in the production process. The accuracy of this method can be affected by many factors, such as the placement of the solder-blocking plate. Unreasonable use of a solder blocking plate will easily lead to solder paste overflow on both sides of the squeegee, and the calculation deviation of solder paste volume in the printing zone will lead to inaccurate solder addition.
Solder paste feeding requirements
When the squeegee is at the last end and in the static state, solder paste can be added automatically. Tin can also be added during printing. When the squeegee moves, add the solder paste in the middle of the squeegee, and the solder paste will spread evenly to both sides as the squeegee moves. The height of the solder paste on the stencil should be controlled within 1/3 to 2/3 of the height of the squeegee. If choosing to add solder paste manually, it is needed to ensure that the solder paste is within the moving route of the squeegee, and the length of the solder paste strip should not exceed the length of the squeegee.
It should be noted that the volume of the solder on the stencil has a significant impact on the printing quality. If the solder is insufficient, the pads will not be fully covered by the solder. However, an excessively amount of solder paste will cause the following problems:
Solder paste slips during printing, reducing the efficiency of filling the stencil apertures;
Solder paste overflows from the top of the squeegee and falls into the printing zone after deterioration, affecting the printing quality;
Longer printing time causes the solder paste viscosity to increase, which is not conducive to printing;
An excessive amount of solder is printed on the pads.
Shenzhen Fitech has rich experience in the production of printing solder pastes and can provide customers with ultrafine printing solder paste products with stable viscosity and excellent printing performance. The solder joint formed after reflow soldering has high mechanical strength and a low volume of voids, which can meet the requirements of high soldering reliability.