BGA Solder Paste and BGA Reballing Processes - Shenzhen Fitech
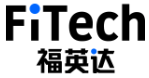
BGA Solder Paste and BGA Reballing Processes - Shenzhen Fitech
With the rapid development of large-scale integrated circuits, traditional packaging technologies such as through-hole packages cannot meet the requirements of high-density packaging. Due to the requirements of high integration, small package size, and more I/O quantities, new packaging processes have emerged. Ball grid array (BGA) packaging has broken through the limitations of traditional packaging and is now a new packaging technology widely used. The common types of BGA reballing include laser reballing, printing solder reballing, manual solder reballing, and pad-printing reballing.
Laser reballing
Laser reballing is mostly used in small-batch BGA package production, with simple operation and short process flow. The mechanism of laser reballing is to put the solder balls into the laser reballing machine. The solder balls reflow inside the machine and melt into liquid separately. The liquid solder will drop onto the BGA pads through the nozzle to complete the laser reballing process. The process needs to be protected by nitrogen to avoid solder oxidation.
Printing solder reballing
The process of printing solder reballing is similar to that of SMT solder paste printing. In the process of printing solder reballing, the small stencil needs to be aligned and positioned on the BGA pads, and then solder paste printing is carried out. After reflow, the solder paste solidifies and shrinks into solder balls. The defect of printing solder reballing is that the uniformity and coplanarity of the solder ball are limited. Solder pastes (T6 and above) have the characteristics of small particle size, which can replace performed solder balls for small-size BGA reballing.
The solder paste printing process is a process in which lead-free solder paste is transferred from the stencil to bonding pads, involving the use of a template, solder paste, and automatic printing machine. The solder paste printing process has a significant influence on the reliability of printing solder reballing. After confirming the amount of solder paste required for BGA reballing, it is necessary to customize the stencil with an appropriate aperture layout. The following factors should be considered when determining the volume of solder paste required for BGA reballing.
1. The solder paste volume should be sufficient to ensure good BGA size.
2. The coplanar error (usually 0.1mm) of the solder ball of BGA components shall be taken into account when determining the volume of solder paste.
3. When other fine-pitch components exist on the PCBs, the solder paste volume should be comprehensively considered to prevent extra soldering defects.
Manual solder reballing
Manual solder reballing is not suitable for mass production but is generally used for BGA repair or BGA sample making. A small stencil is required for manual solder reballing. The stencil is aligned to the pad position, and the solder ball should be placed into the stencil apertures. After the stencil is removed, reflow heating is conducted to melt the solder balls.
Pad-printing reballing
Pad-printing reballing is a mature process to achieve mass production and high efficiency of BGA reballing. Tens of thousands of solder balls can be planted in a few seconds. The process of pad-printing reballing can be roughly divided into the following steps.
1. At the beginning, BGA pads are placed upward on the transfer track. According to the production capacity of the manufacturer, the number of BGAs at a reballing cycle is 4 to 20.
2. Manufacturers need to choose specific needles according to BGA requirements. If each BGA is made of 1000 solder balls, the needle array is composed of 1000 needles. If there are 4 BGAs, 4 needle arrays (4000 needles) are required. The needles are used to dip the solder flux and transfer it to the 4 BGA pads. After pad printing, BGA will be transferred to the next step.
3. BGA solder balls are stacked on the needle, and a vacuum is applied. Each needle picks up a solder ball and aligns it with the BGA pad with solder paste, then turns off the vacuum and blows to separate the solder ball onto the pads. After the solder balls are placed, reflow soldering is completed to melt the solder balls.
Shenzhen Fitech has advanced technology to produce ultrafine solder pastes (T6 and above) that are suitable for BGA reballing process. The solder balls formed by Fitech’s ultrafine solder paste products after reflow soldering have the proper size, high surface smoothness, and excellent mechanical strength, which can be used to replace the preformed solder balls.