Reliability of RFID Anisotropic Conductive Pastes_Shenzhen Fitech
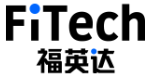
Reliability of RFID Anisotropic Conductive Pastes_Shenzhen Fitech
Anisotropic conductive pastes (ACP) can conduct electricity vertically and do not conduct electricity horizontally. ACP has various solid components, including such as Ag particles, polymers, and solder powder. The curing temperature of ACP ranges from 100 to 200 degrees Celsius. The RFID chips can use ACP when bonding with the substrate, and the electric signal between the chip and the substrate can be realized after soldering. If the curing time is not optimized, the quality of the RFID inlay will deteriorate. Therefore, it is necessary to study the ACP materials and curing conditions that are related to the changes in bonding reliability.
Figure 1. RFID Flip-Chip Bonding Process Using Anisotropic Conductive Paste.
In order to test the soldering effect of RFID chips bonded with ACP, Lee et al. conducted a series of experiments to verify it. Lee et al. applied the anisotropic conductive adhesive on the PET substrate and then aligned the RIFD chip with the pad for placement and hot bar. The bonding is completed after the solder is cured. The methods for manufacturing antenna patterns include copper foil etching and paste-like Ag ink etching.
Table 1. Properties of the experimental anisotropic conductive pastes (ACP-1, ACP-2).
Test result
Table 2 summarizes the bonding strength and fracture surface of antennas bonded with ACP-1 and ACP-2 by considering different antenna materials and bonding time. For the antenna pattern made of copper foil, the shear strength was the minimum when the heating time was 5s. Heating for 10s brought the maximum shear strength (15.7N). When the heating time was 5s, the main fracture structure of the solder joint was delamination. For the antenna pattern made of Ag ink, the shear strength was the highest when the heating time was 10s. In addition, Lee et al. found that when the ACP fully hardened, the insufficient adhesion between Ag ink and PET substrate led to the delamination of antenna patterns. However, the shear strength of the antenna pattern made of Ag ink is 13%-14% higher than that of the antenna made of copper foil.
Table 2. Antenna bonding shear strength and failure surface (ACP-1).
Table 3. Antenna bonding shear strength and failure surface (ACP-2).
After using ACP-2, the shear strength of solder joints was further improved, which was more than 20% higher than that of ACP-1. Therefore, ACP-2 can bring better adhesion. However, similar to ACP-1, the shear strength of ACP-2 declined rapidly after reaching the peak.
Unlike the ACA filled with Ag particles/polymers, Shenzhen Fitech can produce ACP products filled with alloy solder powder. Fitech’s ACP products can be used for semiconductor and microelectronic soldering, with excellent conductivity after soldering. After curing, the epoxy resin composition can provide effective stress and corrosion protection for chips.
Reference
Lee, J.S., Kim, J.K., Kim, M.S., Kang, N. & Lee, J.H. (2011). Reliability of flip-chip bonded RFID die using anisotropic conductive paste hybrid material. Transactions of Nonferrous Metals Society of China, vol. 21, pp.175-181.