Printing Solder Paste_ PCBA Failure Caused by Chemical Corrosion
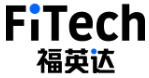
Printing Solder Paste_ PCBA Failure Caused by Chemical Corrosion
PCBA is a process of SMD assembly and through-hole component insertion on PCBs. PCBA is almost everywhere in the microelectronics and semiconductor industries. The high reliability of PCBA requires that every assembly step meets the requirements. However, there are often some unpredictable factors that will cause component failure. For example, residual corrosive substances on PCB are easy to cause chemical corrosion.
Chemical corrosion can be divided into the following categories in principle.
1) Electrochemical migration: Electrochemical corrosion refers to the migration of conductive particles in a certain environment, which eventually leads to short circuits or electric leakage between conductors. When there is a certain degree of humidity and salts in the PCBs, electrochemical migration is easy to occur in the presence of voltage difference.
2) Chemical corrosion: Chemical substances such as inorganic acid, organic acid, and organic salt in solder paste flux will react with PCB pads under humidity conditions. The generated copper salt or cuprous salt has limited influence on the solder joints in a short time, but it will gradually weaken the strength of the solder joints, which increases the risk of short circuits in the later stage of the solder joints.
3) Conductive anodic filament effect (CAF): CAF effect usually occurs in high humidity and high voltage gradient. CAF is a copper salt that grows from anode to cathode along the epoxy glass interface of the PCB. The growth of CAF will cause short circuits and leakage between conductors. When the leakage current is greater than the limit that the CAF can withstand, the CAF will melt and spread nearby, which can participate in the formation of the CAF again.
CAF effect is closely related to water absorption of the material. The order of anti-CAF effect performance is BT>CE>CEM-3>G-10>PI-FR4>aramid fiber>epoxy resin>MC-2. In addition, the CAF effect is also related to the spacing between copper conductor and glass fiber. For small conductor spacing and the short distance between the glass fiber and the copper conductor, the formation rate of CAF is high.
Figure 1. The schematic diagram of CAF.
To reduce corrosion, we should start from all aspects. We should not only select PCB materials but also strictly control the quality of printing solder paste for PCBA. Shenzhen Fitech highly controls the production process of printing solder pastes to ensure the total halogen elements are below 1500 ppm. Moreover, Fitech’s printing solder pastes have good printability, and the strength of solder joints can be kept at a high level for a long time after soldering.