Soldering Reliability of PCB with Immersion Silver Surface Finish_Fitech Solder Paste
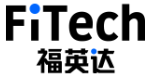
Soldering Reliability of PCB with Immersion Silver Surface Finish
Immersion silver is a process used for PCB surface finish. The bonding pad is immersed into the electroless silver bath for silver plating. The PCB with an immersion silver surface finish is called immersion silver PCB. The production process of the silver plate can be roughly divided into oil removal, washing, micro etching, washing, pre-immersion, silver deposition, oxidation resistance treatment, washing, and drying. In the process of immersion of silver, silver ions obtain electrons, while copper loses electrons and gets oxidized. Eventually, silver will deposit on the pad surface to form a silver layer. Immersion silver PCB is widely used. Usually, solder paste is printed on the PCB, or solder balls are flip-chip bonding on the PCB. The PCB finally experiences a reflow process. During reflow, solder paste/BGA balls melt and solidify to form solder joints.
Solder joints generally require excellent mechanical strength and conductivity. In order to understand the reliability of solder joints on the immersion silver PCB, Yoon and Jung conducted a reflow process for SnAg3.5C0.7 solder balls at 250℃ for 60s to produce solder joints. The reliability test included solder joint aging and shear stress test.
Microstructure of solder joint
After reflow soldering, the silver plating layer and part of the Cu layer dissolved into the molten SnAg3.5C0.7 solder. Dissolved Ag and Cu reacted with the solder at the interface to form intermetallic compounds Cu6Sn5 and Ag3Sn. At the interface between the solder and pad, Cu6Sn5 was mainly rod-shaped, while Ag3Sn was plate-shaped. The intermetallic compounds developed continuously during reflow and aging.
Figure 1. Intermetallic compound of SnAg3.5C0.7 solder joint.
Aging test results
After aging at 150°C for 24 hours, a very thin Cu3Sn layer appeared at the interface between the Cu6Sn5 layer and the Cu pad. In addition, with the increase of aging time, more Cu dissolves into the solder, resulting in continuous growth and thickening of Cu6Sn5 and Cu3Sn layers. Yoon and Jung found that when the aging time of solder joints increased to 2400 hours, the total thickness of Cu6Sn5 and Cu3Sn layers was about 8μm and 3μm, respectively.
Figure 2. Cu6Sn5 and Ag3Sn structures at different aging times. Left: 24 hours; Right: 2400 hours.
Yoon and Jung took the peak shear stress as the standard to measure the mechanical strength of solder joints. The shear stress of solder joints decreased rapidly in the first 24 hours of aging, and then the shear stress decreased significantly. After aging for 500 hours, the shear stress of solder joints became stable.
Figure 3. Peak shear stress change of solder joint after aging.
According to different aging times, solder joint failure mode changes from internal solder fracture to interface fracture. After 250 hours of aging and shear action, the internal part of the solder joint began to fracture. For solder joints aged for 500 hours or longer, failure occurred at the solder/Cu6Sn5 interface. The reason for fracture is due to the excessive growth of brittle intermetallic compounds.
For BGA reballing process, solder paste can be used instead of solder balls. Solder paste is deposited onto the BGA pads by printing. Solder paste shrinks and becomes solder balls after reflow.
The solder paste products produced by Shenzhen Fitech have excellent solderability, which can effectively react with the silver plating layers of the immersion silver PCBs during reflow. The silver rapidly dissolves into the solder paste, and the solder paste cure to form solder joints that have high reliability. Welcome to inquire for more information.
Reference
Yoon, J.W. & Jung, S.B. (2008). Effect of immersion Ag surface finish on interfacial reaction and mechanical reliability of Sn–3.5Ag–0.7Cu solder joint. Journal of Alloys and Compounds, vol.458(1-2), pp.200-207.