Component Solderabilty_ Wetting Balance Test_Shenzhen Fitech
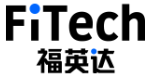
Component Solderabilty_ Wetting Balance Test - Shenzhen Fitech
In order to avoid the problem of insufficient solder volume in component pads/leads during mass production, the industry often conducts solder wetting balance tests on components to verify the component solderability. The wetting balance test can check whether the solderability of PCBA can meet the application requirements, and can determine the cause of poor wettability. The wetting balance test can be divided into the solder ball method and the solder bath method.
The forces of the wetting balance test involve the buoyancy of the solder on the component and the downward tensile force (wetting force) formed when the solder wets the component. The wetting balance test requires fixing the testing component sample on the head of the solder balance, and then applying flux to the test area, and resetting the balance to zero. With the movement of the balance head or the balance platform, the sample will contact the solder. The solder will produce buoyancy after contacting the testing sample, and the buoyancy is specified as negative values. When the solder starts to wet the sample, it will form a downward wetting force on the testing sample, and the wetting force is specified as a positive value. As the wetting process continues, the wetting force will gradually balance with the buoyancy and then exceed the buoyancy.
When the sample starts to leave the solder bath, the buoyancy begins to drop. Once the sample is completely removed from the solder bath, the solder does not exert buoyancy on the sample, and the tensile force is maximum at this time. Finally, the solder will no longer exert tension.
Figure 1. Process of wetting balance test.
Copper sheet tin bath method: A copper sheet is immersed into the flux for 3-5 mm, and the immersion depth in the flux shall be greater than in the tin bath. Table 1 shows the test parameters.
Table 1. Wetting balance test parameters of solder bath method.
4. Interpretation of test results
The shorter the test time, the faster the PCB is wetted. Besides, if the maximum wetting force is large, the wettability of the solder to the base metal is better. The wettability affects the soldering performance. The slow wetting speed requires a longer soldering time, while the longer soldering time will increase the thickness of the intermetallic compound layers, which affects the mechanical strength of the solder joints. For the reflow process, the soak zone of the reflow profile can allow the flux to reduce the oxide layers on the soldering surface, improving the wettability. An excessively short dwell time of the soak zone is not conducive to the improvement of wettability. Hence, the wettability should be fully considered when designing the reflow profile.
5. Solder paste products
Shenzhen Fitech is committed to the research, development, and manufacture of solder powder and ultra-fine solder paste products (T6 and above). Fitech’s lead-free solder powder has high sphericity, narrow particle size distribution, and low oxidation content, which can be used to prepare high-quality solder pastes. In addition, Fitech’s ultra-fine solder paste has excellent wettability and high solder joint strength after reflow, which can meet the requirements of customers for microelectronics soldering. Welcome to contact us for cooperation.