Preparation of Bumps at Formic Acid Atmosphere without Flux_Fitech Solder Paste
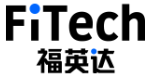
Preparation of Bumps at Formic Acid Atmosphere without Flux_Fitech Solder Paste
It is well known that lead-free solder can achieve a better soldering effect with the aid of fluxes. The fluxes can remove the oxide on the surface of solders and pads to improve the surface tension so that the solder can better wet the pads. However, if the flux is not decomposed sufficiently, it is easy to produce acidic residues, which affects the reliability of electronic components. With the deepening understanding of solder in the industry, many people believe that injecting formic acid during soldering can provide similar effects to flux. As a result, the soldering system can be fluxless. When heating, formic acid can reduce oxides and improve the solder wettability.
1. Principle of oxide reduction by formic acid
Since the major component of solder is Sn, it is easy to be oxidized into SnO and SnO2. Formic acid can react effectively with SnO and SnO2 to form Sn (HCOO)2 that can be further reduced to Sn at 150℃.
2. Soldering test at formic acid atmosphere
In order to verify the feasibility of fluxless soldering in a formic acid atmosphere, He et al. used Sn42Bi58, SAC305, and Sn95Sb5 solder balls to carry out bump preparation on copper pads and nickel-plated copper pads, respectively. The peak soldering temperatures of Sn42Bi58, SAC305, and Sn95Sb5 are 200℃, 250℃, and 275℃, respectively. Subsequently, the bumps were aged at 150℃.
Figure 1. Schematic diagram of soldering at formic acid atmosphere.
Table 1. Five heating conditions used in the experiment.
3. Experimental results
3.1 Contact angle between solder and substrate
The smaller the contact angle between the solder and the substrate, the better the wettability of the solder. The contact angle of Sn42Bi solder soldered under a formic acid atmosphere was smaller than that soldered with flux. However, SAC305 and Sn95Sb5 achieved better contact angles when soldered with flux. In general, the contact angles achieved under a formic acid atmosphere and the assistance of flux were similar.
Figure 2. Conatct angles of solder after solering with formic acid/flux (heating rate: 2.5℃/s, preheat time: 1 min), Sn42Bi58: preheat temperature: 120℃; SAC305 and Sn95Sb5: preheat temperature: 160 ℃.
3.2 Effect of preheating on soldering at formic acid atmosphere
If setting heating speed, peak temperature, and peak heating time as constant, the contact angle between SAC305 solder and substrate was the smallest when the solder was preheated at 160 ℃ for 10 minutes. The contact angle was the largest when preheating at 160 ℃ for 1 minute. A long preheat time allows formic acid to sufficiently react with solders and pads to remove oxides. In addition, the contact angle is related to the preheat temperature. A higher preheat temperature can accelerate the reaction of formic acid and oxides.
Figure 3. Effect of preheat on contact angle obtained after soldering with formic acid .
3.3 Intermetallic compounds
In order to study the intermetallic compounds (IMCs) produced in a formic acid atmosphere, He et al. observed the microstructure of SAC305 solder joints. He et al. found that the IMC obtained when soldering with formic acid or flux-assisted condition was Cu6Sn5, and Cu3Sn was formed when aging. Besides, the total IMC thickness has little difference.
In order to meet the solder material demands of the packaging industry, Shenzhen Fitech has invested a massive number of resources in the research, development, and production of solder powder and solder paste. Fitech’s solder paste has stable viscosity, long stencil time, and excellent wettability, which can meet customers' requirements for high soldering standards. Welcome customers to cooperate with us.
4. Reference
He, S.L., Bi, Y.H., Shen, Y.A., Chen, Z.K., Gao, Y., Hu, C.A & Nishikawa, H. Contact angle analysis and intermetallic compounds formation between solders and substrates under formic acid atmosphere. Journal of Advanced Joining Processes, vol. 6.