The Parameters Affecting Centrifugal Atomized Solder Powder_Shenzhen Fitech
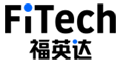
The Parameters Affecting Centrifugal Atomized Solder Powder_Shenzhen Fitech
Semiconductor packaging processes such as SMT, BGA, solid crystal, etc. often use solder paste. Solder paste is composed of solder powder and flux. The highest proportion is solder powder. Therefore, the performance of solder powder, such as oxygen content and sphericity, will have a significant impact on the reliability of solder paste. There are two types of solder powder preparation technologies on the market: ultrasonic atomization and centrifugal atomization, among which centrifugal atomization is the topic of this article. The operating parameters of a centrifugal atomizer include rotational speed, molten metal feed rate, shape and size of the atomizer, oxygen content, etc. During the centrifugal atomization process, molten metal collides with a high-speed rotating disc and diffuses radially due to centrifugal force. The moving molten metal forms a thin film on the surface of the turntable. Ideally, the molten metal film begins to disintegrate and form small droplets at the edge of the atomizer.
A conventional centrifugal atomizer consists of a tundish, atomization device, atomization chamber, and atmosphere control device. Plookphol et al. analyzed the parameters that affect the characteristics of SAC305 solder powder, such as feed rate, rotating speed, atomizer shape, and the influence of oxygen content on the median particle size and yield of SAC305 powder. After preheating the experimental atomization disk to 180°C, turn on the high-speed motor and adjust it to the predetermined speed by adjusting the power supply voltage on the motor terminals. The molten alloy from the pouring plate is then transported to the rotating atomizing plate through a nozzle.
Figure 1. Experimental centrifugal atomization equipment.
The influence of centrifugal atomization parameters
Rotating speed and feed rate
The particle size of SAC305 powder tends to become finer with increasing rotational speed. From Figure 2, when the rotational speed reaches 25000 rpm, the rate of particle size change begins to become very small. Improper feeding rate can cause discontinuous flow and premature solidification of molten solder on the atomizer. The experimental results indicate that the median particle size of SAC305 powder increases with a higher feed rate. At higher feed rates, the thickness of the melt film becomes thicker, resulting in coarser broken particles. In addition, a higher feed rate leads to more melt sliding, resulting in a slower flow rate of the melt film.
Figure 2. Effect of rotating speed on powder particle size (50mm flat disc atomizer, feeding speed 32kg/h, molten solder temperature 318 ℃).
Figure 3. Effect of feed rate on powder particle size (50mm flat disc atomizer, rotating speed 20000rpm, molten solder temperature 318℃).
Atomizer shape and oxygen content
Atomizer shape also has an impact on particle size. Compared to the flat disk atomizer, the SAC305 powder prepared by the cup-shaped atomizer has a smaller particle size. As the diameter of the atomizer increases, the particle size of the powder becomes smaller. An atomizer with sloping edges will help to further diffuse the molten film onto the surface of the disc. Therefore, the atomized droplets will disperse at a higher speed from the atomizer and can continue to decompose during flight. Oxygen will cause oxidation on the surface of molten SAC305 droplets, which should prevent the required continuous decomposition into smaller droplets. The median size of SAC305 powder decreases with a decrease in oxygen content in the atomization chamber. After oxygen content is below 10 vol.%, the particle size is slightly affected. To achieve a better SAC305 state, the oxygen content should be controlled at a low level.
Figure 4. The effect of oxygen content in the atomization chamber on powder particle size (40mm cup-shaped atomizer, rotating speed 30000rpm, feed rate 32kg/h, melting solder temperature 318℃).
Fitech's solder powder
Fitech has rich experience in solder powder preparation and advanced powder production lines, capable of producing conventional and ultra-fine solder powder materials (T2-T10). Fitech has made significant improvements to the existing atomization technology in the industry, making the oxygen content, sphericity, and particle size distribution of solder powder at the leading level in the industry. Welcome customers to purchase solder powder from our site.
Reference
Pkloophol, T., Wisutmethangoon, S. & Gonsrang, S. Influence of process parameters on SAC305 lead-free solder powder produced by centrifugal atomization. Powder Technology, vol.214.