Lead-Free Solder Paste_ Metallurgical Bonding of Semiconductor and Solder Paste
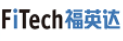
https://en.szfitech.com/
Lead-Free Solder Paste: Metallurgical Bonding of Semiconductor and Solder Paste
The packaging process of microelectronics and semiconductors is to realize the electrical and thermal signals between the chips and PCBs. Solder paste is usually used as the filler between chips and PCBs. After the lead-free solder paste is applied onto the base metal by printing, dispensing, or jetting and the components are mounted, the manufacturers can conduct the reflow process to complete soldering. A series of reactions will occur between lead-free solder paste and base metal during reflow soldering. For example, the solder flux will change the surface tension of the base metals and solder paste, which allows the solder to spread on the pads. Meanwhile, the flux can reduce the oxide on the pads. Finally, the solder paste will have a metallurgical reaction with the pads under the heating conditions to achieve bonding. Let’s talk about metallurgical bonding.
Metallurgical bonding mechanism
The high mechanical strength of the solder joint depends on excellent metallurgical bonding. Metallurgical bonding refers to the formation of atomic metallurgical bonding between lead-free solder paste and base metals by heating. Metallurgical bonding is essentially achieved by atomic diffusion. Solder alloy and Cu atoms in pads diffuse and consume under heating, forming specific intermetallic compounds (IMCs) at the interface between the solder layers and pads. The IMCs will nucleate and grow, achieving a metallurgical bonding between the solder layers and the pads. Phase diagrams can determine the types of IMCs.
For example, when SnAg3Cu0.5 lead-free solder paste and Cu pads are used for soldering, Cu atoms will conduct grain boundary diffusion to the interface between the solder layers and pads. Then the Cu atoms will dissolve into the solder layer, producing a continuous IMC layer at the interface with the Sn atoms in a specific atomic proportion. Due to sufficient Sn atoms in lead-free solder paste during reflow soldering, the main IMC formed is Cu6Sn5. Cu6Sn5 will gradually ripen into a scallop shape during the growth process (Fig. 1). As time goes on, another IMC called Cu3Sn will also be generated. The emergence of Cu3Sn is accompanied by the consumption of Sn and Cu6Sn5.
Figure 1. IMC growth of SAC305 soldering (Lee and Mohamad, 2013).
In addition to Cu6Sn5 and Cu3Sn, Sn and Ag in the molten solder paste also react during reflow soldering. Thus, a small amount of Ag3Sn in the solder paste layer is accumulated. After the lead-free solder paste is cured, Ag3Sn is evenly distributed near the IMC layers. The growth of Ag3Sn is related to the Ag content in the solder paste. When the Ag content in the solder paste is above 4wt%, large pieces of Ag3Sn will appear.
Influences of Solder Paste Volume and Reflow Time on Metallurgical Bonding
The types and quantity of IMCs generated during metallurgical bonding depend on the metal composition and quantity of the solder paste. When the solder paste is sufficient, Sn continues to diffuse to the Cu pad interface, and the Cu6Sn5 layer becomes thicker. Besides, the solder paste with high Sn contents will produce spheroid Cu6Sn5 during soldering.
With the increase of reflow time, Sn will be gradually consumed, and the diffusion rate of Sn becomes slower. Consequently, the thickness of the Cu6Sn5 layer tends to be stable, followed by the growth of Cu3Sn IMC. The total IMC thickness will continue to increase. Generally, Sn will be completely consumed during thermal aging, and Cu6Sn5 will start to decompose and form more Cu3Sn adjacent to the Cu pads. The influence of excessive growth of Cu3Sn is negative, which will make the solder joints vulnerable to brittle fracture.
Figure 2. IMC growth of SAC305-Cu pad interface at different reflow duration (Lee and Mohamad, 2013).
Shenzhen Fitech can provide solder paste products suitable for the reflow soldering process. Moreover, Fitech can provide clients with advice on reflow profiles to precisely control the IMC layer thickness and improve the performance of solder joints.
Reference
Lee, L.M. & Mohamad, A.A. (2013). “Interfacial Reaction of Sn-Ag-Cu Lead-Free Solder Alloy on Cu: A Review”. Advances in Materials Science and Engineering.