Epoxy Solder Paste_ Solder for Automobile Electronic Packaging
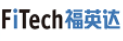
https://en.szfitech.com/
Epoxy Solder Paste_ Solder for Automobile Electronic Packaging
With the development of automobile technology, people put forward higher requirements for the performance of automobiles, leading to a higher integration degree of the automotive electronic control system. The increased integration of automobile electronic control is accompanied by the improvement of packaging difficulty and reliability requirements, which requires higher requirements for packaging materials. The traditional rosin-based solder paste is easy to generate corrosive residues after soldering, which will cause damage to automotive components, and the solder joint strength is insufficient. The difference is that the epoxy solder paste will be cured to form a thermosetting adhesive after soldering. The solder joint is unnecessary to clean, and the corrosion problem is also alleviated. Therefore, the application of epoxy solder paste in automotive electronics has become widespread. This article will introduce the performance of epoxy solder paste in the automotive electronics package.
Sharma et al. mixed T4 SAC305 alloy powder and epoxy flux to prepare SAC305 epoxy solder paste. The epoxy solder paste was used for the packaging of an automotive-graded 1608 resistor. The peak reflow temperature was controlled at 240 ℃. After completing reflow soldering, Sharma et al. carried out a thermal cycle test (- 40-125 ℃), shear strength test, and surface insulation resistance test of the solder joint.
Figure 1. Structural diagram of 1608 resistor solder joints. (a) Before reflow; (b) After reflow (Sharma et al., 2017).
Experimental result
Thermal cycle test
It can be seen from Figure 2 that the solder joint fillet of the 1608 resistor was tightly wrapped by cured epoxy resin before thermal cycling. When conducting 250 thermal cycles, the epoxy resin coating effect was still considerable. However, as the number of thermal cycles increased to more than 500, the epoxy resin layer gradually melted and collapsed, and the solder joints began to be exposed. IMCs of Ag3Sn and Cu6Sn5 coarsened, and their thickness increased with the thermal cycles. At the same time, after 750 thermal cycles, the nucleation and growth of voids in the solder layer were observed.
Figure 2. Thermal cycle test of 1608 resistor solder joints (Sharma et al., 2017).
In order to study the influences of epoxy resin on the growth of IMCs, Sharma et al. compared the soldering effects of rosin solder paste (SAC305) and epoxy solder paste (SAC305E). The results showed that the growth rate of the Cu6Sn5 layer of the SAC305E sample was slow, while the Cu6Sn5 layer of the SAC305 sample increased rapidly after 500 thermal cycles (Figure 3). It is important that the IMC thickness of the SAC305E sample was less than that of the SAC305 sample after 1000 thermal cycles.
Figure 3. Comparison of soldering effects between SAC305 and SAC305E (Sharma et al., 2017).
Shear strength test
The initial shear force of epoxy-coated solder joints reached 45N and decreased with the increase of thermal cycles. After 1000 thermal cycles, the shear force of epoxy-coated solder joints decreased to 35N, but still higher than 29N of rosin solder paste. It can be known that IMC growth will lead to a brittle solder joint, which will have a negative impact on the shear strength. The high strength of the epoxy-coated solder joint after thermal aging is due to the thermosetting adhesive formed to tightly wrap the solder joint, which not only reduces the impact of aging on IMC growth but also provides extra strength enhancement for the solder joint.
Figure. 4 Change of shear strength of epoxy-coated solder joints.
In the surface insulation resistance test, Sharma et al. found that the insulation resistance of the epoxy flux near the fillet of the solder joint was higher, which means that fewer flux residues were generated. Therefore, less corrosion happens to the solder joint.
Shenzhen Fitech can produce ultra-fine epoxy solder paste/adhesive products such as the SnBiAg alloy series and SnAgCu alloy series for automotive electronics. The products are produced by no-clean formulations and have excellent reliability after soldering. Welcome to contact us for more information.
Reference
Sharma, A., Jang, Y.J., Kim, J.B. & Jung, J.P. (2017). “Thermal cycling, shear and insulating characteristics of epoxy embedded Sn-3.0Ag-0.5Cu (SAC305) solder paste for automotive applications”. Journal of Alloys and Compounds, vol.704, pp.795-803.