Through-Hole Component Introduction_Fitech’s Solder Paste
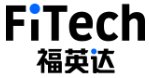
Through-Hole Component Introduction_Fitech’s Solder Paste
When it comes to electronic circuits, we must talk about the electronic components soldered on PCBs. At present, most electronic circuits are composed of surface-mounted components. The mounting method of such electronic components is relatively simple. The conductive pads formed on the surface of the mounting component connect to the pads of the substrates, and the lead-free solder paste is used for soldering. The predecessor of surface mounting technology (SMT) is through-hole technology (THT). THM components usually have leads that can be inserted into specific plated holes on the PCBs and soldered. Although THT has become out of date, it is still used on some occasions, such as the soldering of high-stress connectors. Therefore, we still need to be concerned about the assembly technology of THT components.
Dual Inline Package Structure
The Dual In-Line Package (DIP) is a common through-hole component. DIP carries out the wire-bonding process on the chip to connect the chips and the leads to realize the circuit connection and then inserts and solders the leads into the through holes of the PCBs by using lead-free solder paste to realize the electrical signal. To protect the chips from stress and external environment interference, DIP also uses plastic or ceramic encapsulation for protection.
Figure 1. Through-hole integrated circuit - DIP.
DIP Soldering
Through-hole components have flexible or rigid leads. The flexible leads can be bent and cut into proper sizes according to the plated hole position of the PCBs. For through-hole components with rigid leads, the through-hole in the circuit board needs to be designed in advance. The aim of THT is to insert component leads into the through holes and solder them with pads on the other side of the PCBs. For PCBs containing both SMT and DIP, in order to synchronize with SMT reflow soldering, DIP through-hole reflow are under development. Stencil printing is an effective way to deposit lead-free solder paste on PCBs. Unlike SMT, DIP soldering requires that lead-free solder paste be directly printed into the plated hole without using copper pads. In addition, DIP requires higher volume solder paste to fill the plated holes. Once the leads are inserted into the plated holes, the solder paste will be extruded. After melting, these extruded lead-free solder pastes will penetrate into the through-hole through capillarity and become solder joints.
Figure 2. Schematic diagram of DIP components after soldering.
Figure 3. Through-hole reflow process.
It should be noted that reflow soldering does not apply to all THT components. Due to the poor heat resistance of most THT components and the high melting point of lead-free solder paste, reflow soldering heating the entire component is easy to cause component damage. In addition, it is difficult to control the appropriate volume of solder paste for through-hole reflow, resulting in a poor soldering effect. Therefore, wave soldering is still used in most cases. The reflow process is only used for specific high-temperature resistant in-line components. For customers with through-hole reflow requirements, Fitech can provide highly reliable lead-free solder paste for soldering. Welcome to contact us.