Introduction of Through-Hole Reflow Soldering
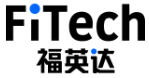
Introduction of Through-Hole Reflow Soldering
Through-hole technology (THT) is a relatively old-fashioned assembly technology of electronic components. The THT needs to open a set number of plated holes with specific sizes on the PCBs. The leads of through-hole (TH) components are inserted into these plated holes to achieve the assembly goal. Obviously, the size of the plated holes must be slightly larger than the component leads for insertion purposes. The uses of THT become relatively rare now because the large size of the TH components makes them difficult to be used for high-density and fine-pitch packaging.
Compatibility of reflow and wave soldering processes
Although the application of TH components is gradually decreasing, it is still indispensable in some fields where passive components (resistors, capacitors, etc.) are used. Wave soldering is generally used for the soldering of TH components. This local-heating technology can protect the component body from high temperatures. However, there are advantages and disadvantages. Wave soldering requires a massive amount of melted solders. At present, the mainstream assembly method is surface mount technology (SMT), and the integral-heating reflow soldering process is mostly used for the SMT components. The reflow process and wave soldering process generally do not coexist. If there are TH components and SMT components on the PCBs at the same time, using different soldering processes separately will result in a waste of resources.
The chips inside the TH components are fragile and need to be encapsulated. The encapsulation material can be ceramic or plastic. Ceramics are high temperature resistant but are high cost and usually used in high-end chip packaging. Plastic packaging is the most common, but it is generally not resistant to high temperatures, so wave soldering has become a technology that has to be adopted. To be compatible with the reflow process of SMT components, many developers in the industry try to realize the reflow technology of TH components.
TH component reflow soldering
TH components need to have a certain high-temperature resistance to complete reflow. At present, the mainstream reflow solder pastes include low-temperature SnBiAg series (melting point of about 139 ℃) and medium-temperature SnAgCu series (melting point of about 217 ℃). Pin-in-paste reflow process can be used for some suitable through-hole components. The TH reflow is similar to the conventional reflow. The lead-free solder paste needs to be printed inside the plated hole for TH reflow. This process is affected by the printing speed, printing angle, and the diameter of the plated hole. The printing quality will significantly affect the solder joint strength. Thus, these parameters need to be accurately designed according to the actual situation.
Figure 1. Through-hole reflow solder paste printing process.
After the solder paste is successfully printed into the plated holes, the automatic placement machine picks up the TH component and inserts it into the plated holes. The leads of the through-hole components tear the solder paste in the plated holes and push a part of the solder paste to the bottom of the PCBs. When reflow soldering, the melted solder paste at the bottom will flow back to the plated holes through capillarity to completely fill the inner section of the plated holes (Figure 2).
Figure 2. Through-hole component placement and soldering process.
Difficulties in THT reflow soldering
TH reflow technology has high requirements for the parameter setting of the printing process and the quality of solder paste. However, the solder paste filling condition inside the plated holes cannot be inspected by the solder paste detector. One of the reasons for the slow promotion of TH reflow soldering is the lack of comprehensive online inspection of the through-hole filling rate. The amount of solder paste significantly affects the filling rate. However, due to changes in leads and reflow parameters, the volume of solder joints is difficult to predict and calculate. In order to improve the accuracy of the amount of solder paste at the plated holes, the step stencil can be used. This step technology can selectively increase or decrease the thickness of certain areas of the stencil to control the local amount of solder paste. The optimal printing speed and printing angle often need to be analyzed through numerical modeling. In addition, the formulation of the solder paste determines the wettability. If the wettability is poor, the solder paste is difficult to fill the plated holes.
For information about solder paste products, please consult Shenzhen Fitech. Fitech has rich experience in the production and application of solder paste and can provide customers with solder products and use advice.