Surface Mount Component Introduction_Shenzhen Fitech
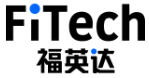
Surface Mount Component Introduction_Shenzhen Fitech
The traditional components adopting through-hole technology (THT) have a large volume and weight, which has been challenged to meet the current industrial requirements of chip miniaturization and large package density. Thus, a new packaging method is needed. The appearance of surface mount technology (SMT) can significantly reduce the volume of electronic components, which allows them better meet the requirements of miniaturization packaging. Currently, when a circuit system is disassembled, it can be found that most of the components are surface mount components (about 90%), and only a low number of through-hole components are used to realize plug connectors, high-power equipment, etc. This article will introduce you to the basic characteristics and soldering process of the SMT components.
Introduction of SMT components
SMT components are directly captured by the vacuum feeder and placed on the surface of PCBs, which is different from the through-hole connection of THT components. Besides, most SMT components are fixed on the PCBs by reflow soldering, while THT components are mainly soldered by wave soldering. SMT components do not use an in-line lead structure but adopt short bent lead or no pin structure with solderable metalized terminals on the side or bottom of the packages. Figure 1 shows a structure diagram of an integrated circuit with leads. It can be seen that the internal chips are bonded with the leads through gold wires. After the components are mounted on the PCB surface, gull-wing-shaped leads will be metallurgically bonded with lead-free solder paste through reflow to achieve electrical signals.
Figure 1. Perspective view of an SO type integrated circuit.
For leadless SMT components such as quad flat no-lead package (QFN), it can save more space and achieve a higher density package. There are several pads around the bottom of the QFN. The conductive paths between these pads and the leads inside the QFN are short, providing the QFN with better electrical performance. The exposed pads are aligned and placed on the solder paste on the PCBs, and solder joints are formed by reflow soldering.
Figure 2. QFN soldering structure.
Some regular SMT component sizes are shown in the table below. The SMT component code usually represents the length and width of the component. For example, the dimension of component 0402 is 0.4mm x 0.2mm (length x width).
Table 1. Some conventional SMT component sizes.
SMT component soldering
Lead-free solder paste is one of the bonding materials widely used for SMT component soldering, which can be printed on PCB pads through stencils. The production methods of stencils include chemical etching, laser cutting, and electroforming. The apertures formed by the electroforming process are the smoothest, and the printing effect is the best. Electroformed stencil is suitable for ultra-fine-pitch soldering, but the stencil cost is high. The smoothness of chemical etching and laser cutting stencils is slightly poor, but the cost is relatively low. The stencil production process shall be selected according to the actual requirement. The stencil apertures are designed according to the PCB pad layout. After the lead-free solder paste is printed, SMT components are captured by the feeder and aligned with the PCB pad position, and then placed on the lead-free solder paste. For SMT components with leads, lead-free solder paste can bond the component leads with PCB pads to form solder joints. In order to ensure high soldering quality, the amount and formula of solder paste need to be accurately controlled.
Figure 3. Schematic diagram of an SMT component after soldering.
Shenzhen Fitech can provide lead-free solder paste products for SMT component soldering, and the ultra-fine solder paste products (T6 and above) can realize ultra-fine-pitch soldering. Fitech can also provide solder paste solutions for customers.